Alessandro Zomparelli is a talented computational designer with a diverse background in Engineering and Architecture. His passion for exploring the possibilities of 3D printing technology has led him to work on projects ranging from architecture to human body extensions. Alessandro has contributed to the Reefs project as a member of Co-de-iT since 2011 and has taught computational design workshops internationally. In 2022, he co-founded MHOX, a generative design studio that creates fashion and medical products that blur the line between body and design.
Alessandro Zomparelli has also taught at esteemed institutions like the Academy of Fine Arts in Bologna and Istituto Marangoni in Milan between 2016-2020. He recently joined the CREATE group as a research fellow, where he is currently exploring architectural geometry and digital fabrication. Alessandro is highly regarded for his work on open-source Blender add-ons like Tissue, which simplify computational design workflows. Currently, he is collaborating on diverse computational design projects and teaching in various international programs.
If you’re curious to learn more about the works of Alessandro Zomparelli, Blender, and Tissue add-on, check out PAACADEMY’s Topology-Based Modelling With Blender / Studio Alessandro Zomparelli!
Serra Utkum Ikiz (PA): How did you start with Blender, and what drew you to use it as your primary software?
Alessandro Zomparelli: I started using Blender during my studies at university. I had courses about other modeling software, but I was annoyed by how heavy they were and the issues related to their licenses. What I immediately liked about Blender was its open-source nature. There were many missing features back then; it was only seven megabytes, but the mesh modeling workflow was really smart and efficient thanks to the various shortcuts.
Over the years it started to grow really fast, and when I started to get confident with its scripting capabilities, I started to customize some tools and replace some of the workflows I used in other software pieces. At some point, I started to collect some of those tools as an add-on that I named Tissue. I decided to share it as open-source to encourage other architects and computational designers to join Blender’s community. Of course, I still use some other software for more complex architectural projects. Still, I really like to use Blender in the preliminary phases, because of its hybrid modeling approach implicit-explicit. In addition to that, for some specific fabrication processes, like 3D printing, it can be really helpful.
Serra (PA): Can you tell us about a few projects you’ve created using Blender?
Alessandro: I have used Blender in various projects, initially mostly related to designing and fabricating fashion accessories or medical devices. Thanks to the various modifiers it is relatively easy to generate complex shapes that follow the body’s anatomy. Together with Bruno Demasi, I also used Blender to design some 3D Printed Clay pieces. We called this series of experiments Clay-Code and the technical challenge was to work entirely with Blender. In order to do that we had to develop some missing pieces, like for example the Gcode Exporter add-on, but as often happens in the open-source community, the struggle of one can become a new tool for many.
For architectural design instead, I found it particularly useful in sketching design ideas or quickly testing some form-finding design. Of course, its great rendering capabilities are just the cherry on top, which helps to communicate the project effectively.
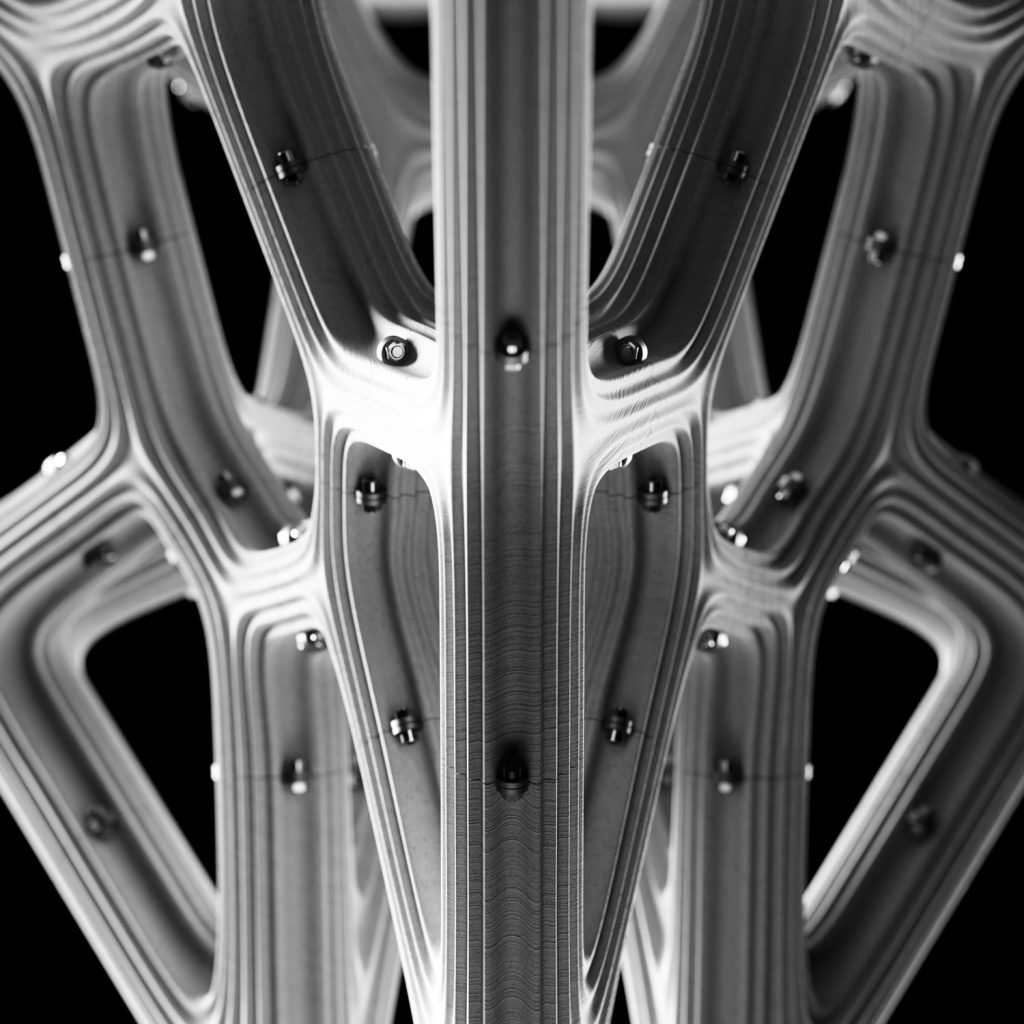
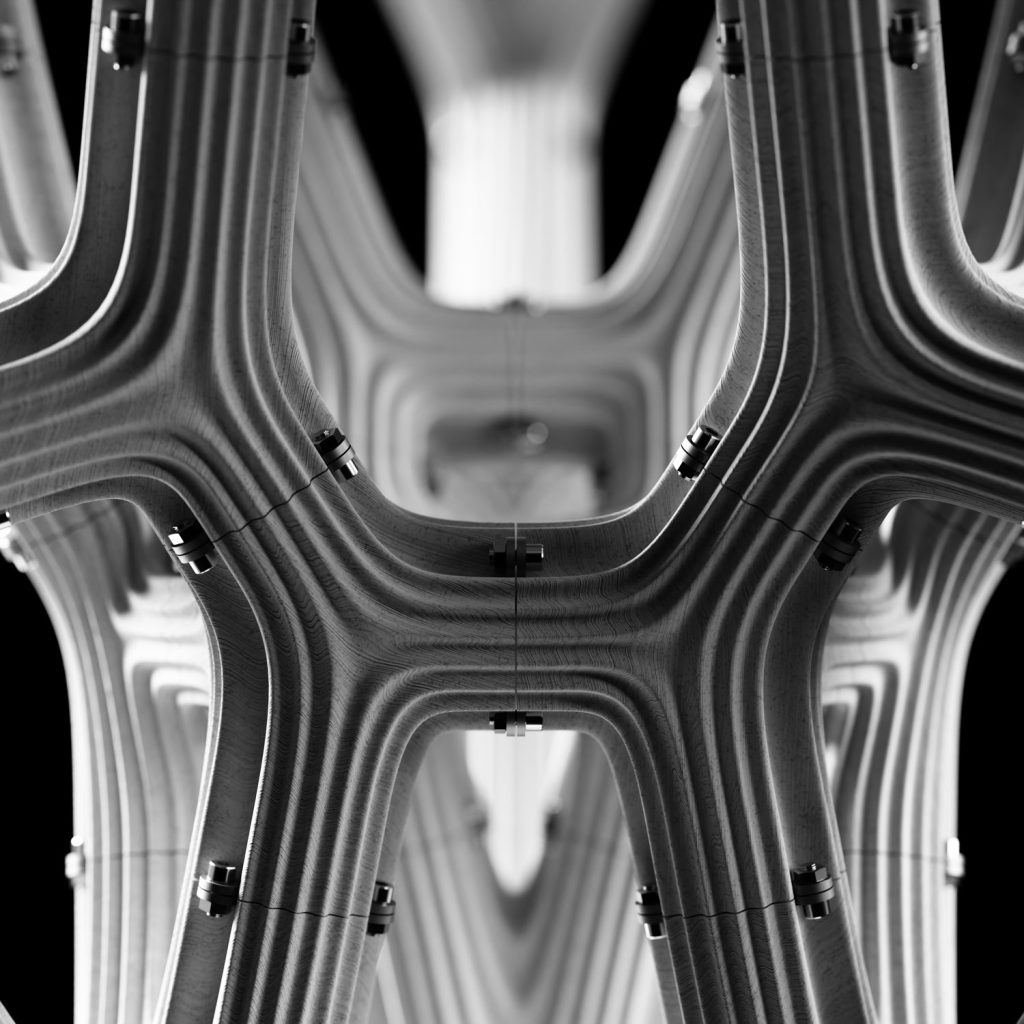
Serra (PA): How did your background in engineering and architecture influence your exploration of computational design and 3D printing?
Alessandro: I think that a background in both engineering and architecture helped me develop competencies in both 3D modeling and design, together with a strong understanding of mathematics. I found out that these competencies together are scarce in other industries, like art, fashion, or medicine. Thanks to 3D printing I found a fertile ground for a growth transversal to the different industries. While I still keep my roots in the Architecture realm, I found myself collaborating on many different design challenges.
Serra (PA): Can you give us some examples of specific projects or scenarios where you found the Tissue add-on particularly useful? How did it contribute to the success of those projects?
Alessandro: During the AA Visiting School in Dubai, the topic of the workshop was additive stereotomy. Using the cloth simulation in Blender, I was able to define a form-finding workflow for a scale pavilion. Since we wanted to build a scale model using 3D-printed interlocked modules, with Tissue, the students were able to use some of the dedicated features to model such complex conditions with a relatively simple approach. This allowed them to focus on the design aspects, rather than dealing with unnecessary complexity.
At SDU (University of Southern Denmark) as CREATE Group we recently worked on design and fabrication strategies for complex polyhedral structures. We developed a topology-based workflow for the creation of 3D printable formworks for concrete components. Thanks to the Tessellation tool, we were able to embed the complexity of the formwork into a few different components. That allowed us to easily interact with the design through a combination of manual modeling and non-destructive operations. We simultaneously evaluated the final piece’s design and the formwork’s shape. The topology-based logic has been quite useful in defining a robust workflow where shape and details were designed and generated at the same time.
In the same context, we also used Blender and Tissue as part of the workflow during the Summer School 2022. We designed two structurally efficient concrete slabs during the workshop with the students. The slabs there were produced using styrofoam milled using a robot and concrete casting. The workflow was complex and involved different steps, like stress analysis, an efficient ribbing pattern design, rebars bending using an AR visor, and robot toolpath optimization.
For this project, Tissue was deployed for its Reaction-Diffusion simulation in order to orient a structural pattern based on the directions and the intensity of the principal moments. This was possible thanks to the anisotropic behavior introduced in the add-on appositely for the workshop. After studying and understanding the relationship between the input information from the stress analysis and the parameter of the Reaction-Diffusion simulation, they were able to test several different options before converging to the final design for the fabrication.
Leave a comment