At Expo 2025 in Osaka, Japanese firm Aki Hamada Architects has unveiled a striking 3D-printed rest facility that reimagines public space through sustainable materials and robotic construction. Developed as part of a broader national initiative featuring 20 pavilions by emerging Japanese architects, the installation combines organic form-making with traditional building methods to create a structure that invites pause, interaction, and reflection.
The project was constructed using the Crane WASP Stand Alone, a large-scale 3D printing system provided by Italian company WASP, known for their innovative work in sustainable architecture. The rest facility incorporates seating areas, toilets, a satellite studio, and a small stage, organized within an earthy, canyon-inspired composition made almost entirely of soil-based materials.
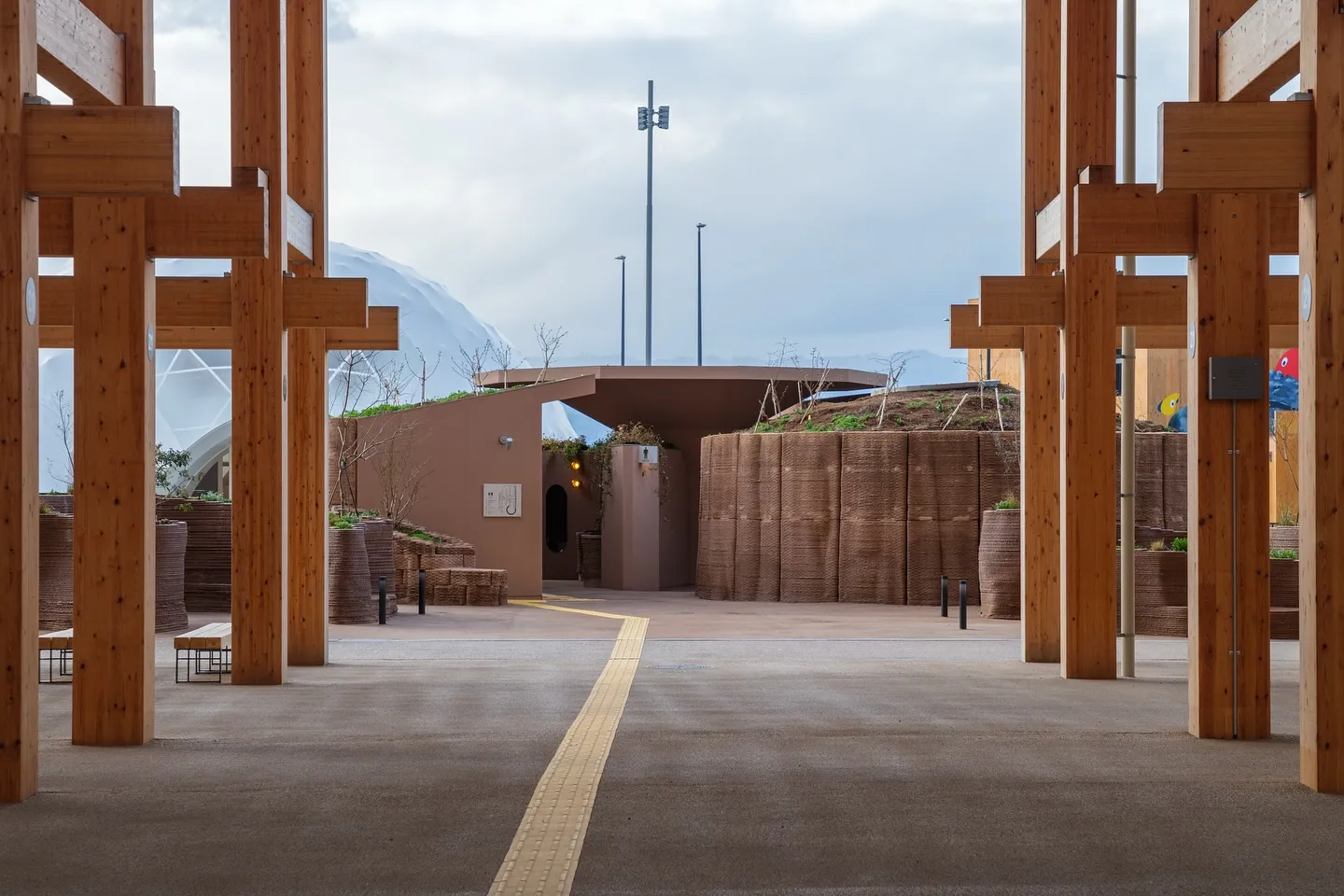
At the core of the construction is a locally sourced soil mix, composed of clay, straw, seaweed glue, pigments, and a magnesium oxide-based hardener. The materials not only honor Japan’s legacy of earthen wall construction but also offer a fully biodegradable solution that can decompose or be disassembled post-event with no lasting environmental impact.
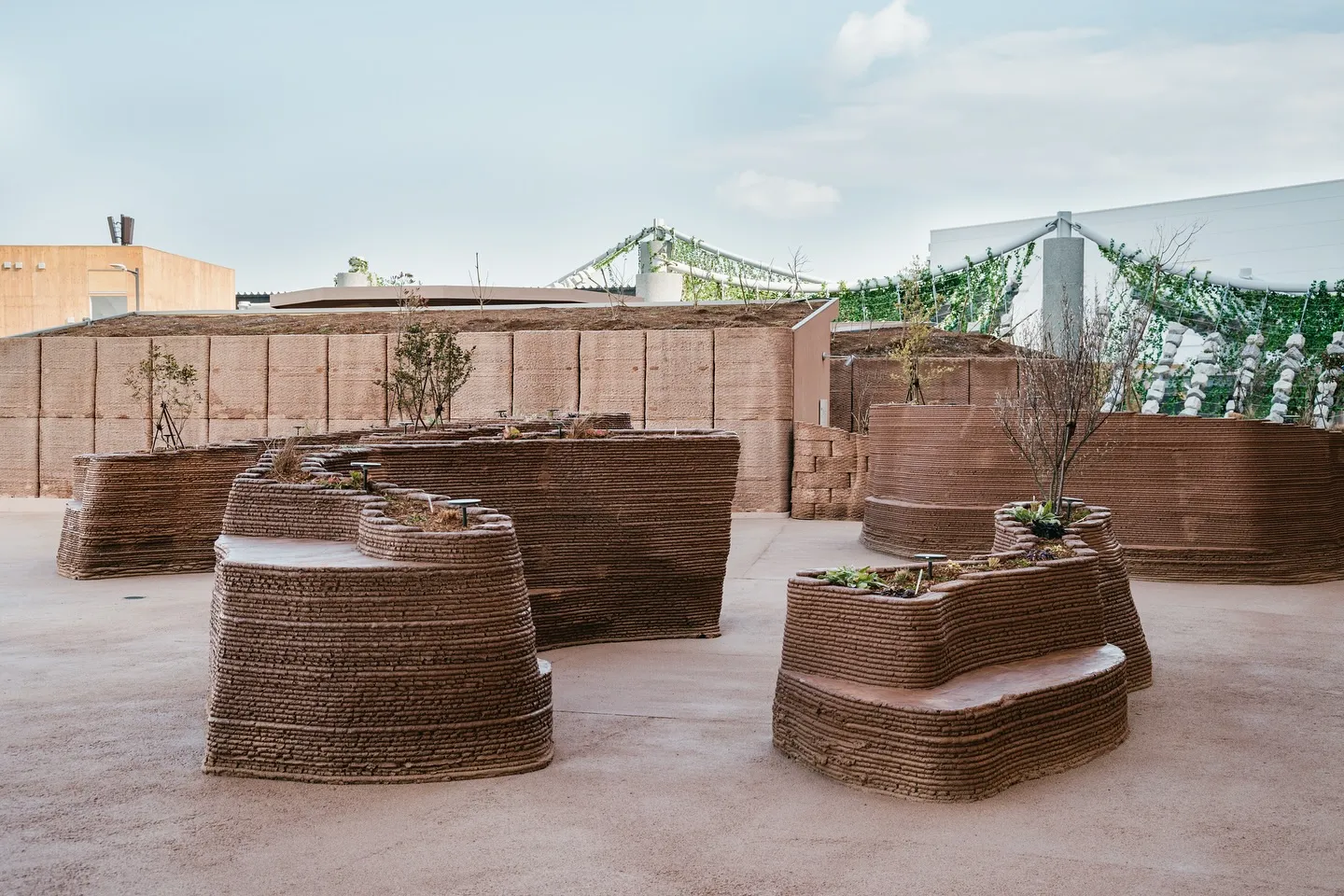
All printed components, ranging from exterior wall panels and benches to cylindrical washbasin, were produced using WASP’s 3D printer, both onsite and at a facility in Toyama. Each element was cured for three days in a humid environment, then air-dried to achieve structural strength. Timber framing and wooden inserts were used to anchor the panels, enabling modular assembly on-site.
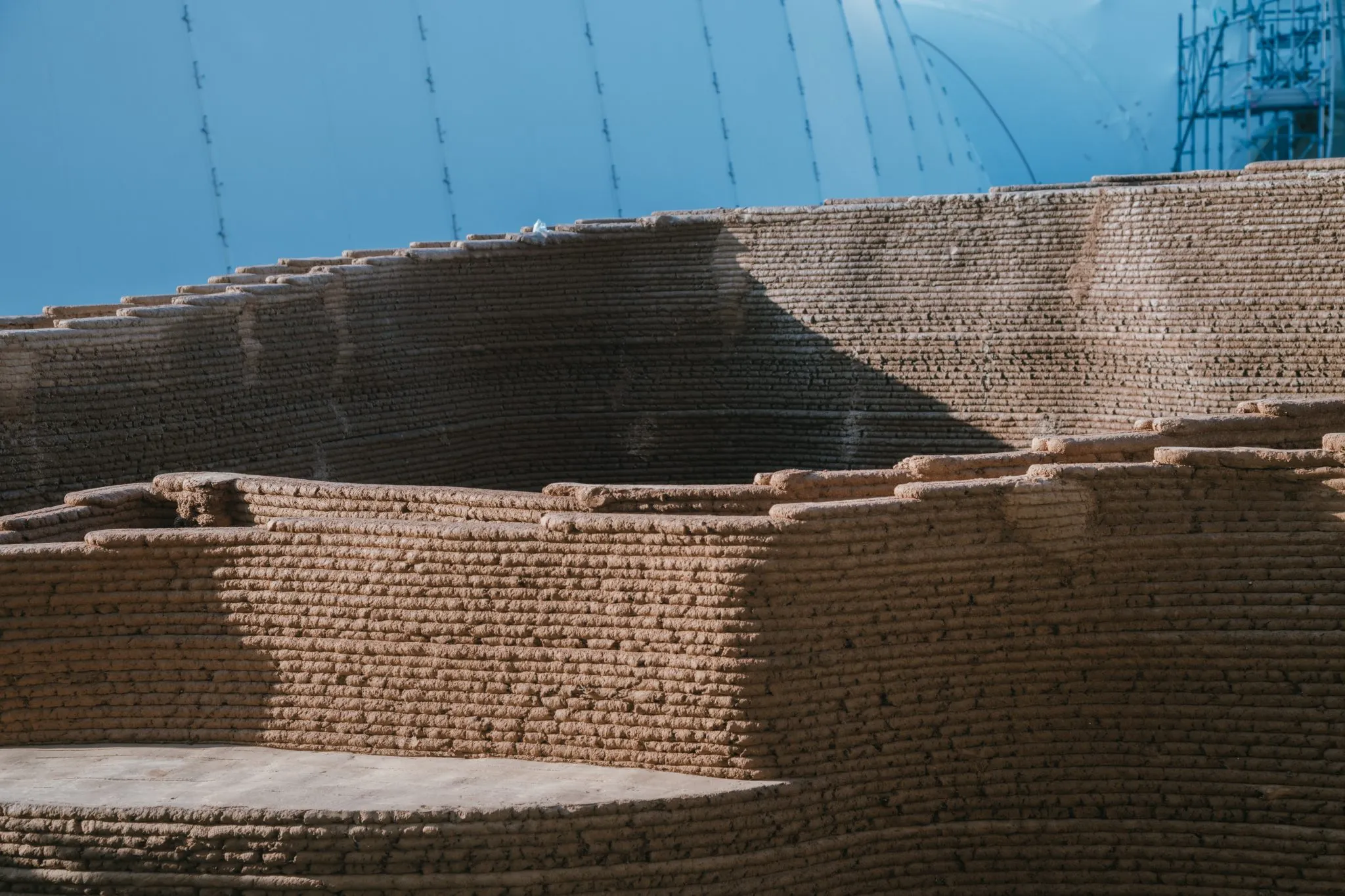
The design draws direct inspiration from Japan’s geological landscape. The architects 3D scanned rock forms from across the country, generating composite geometries that were physically tested to ensure stability using soil alone. These shapes were digitally optimized to meet 3D printing tolerances, allowing the production of curved walls, clustered islands, and semi-enclosed seating zones.
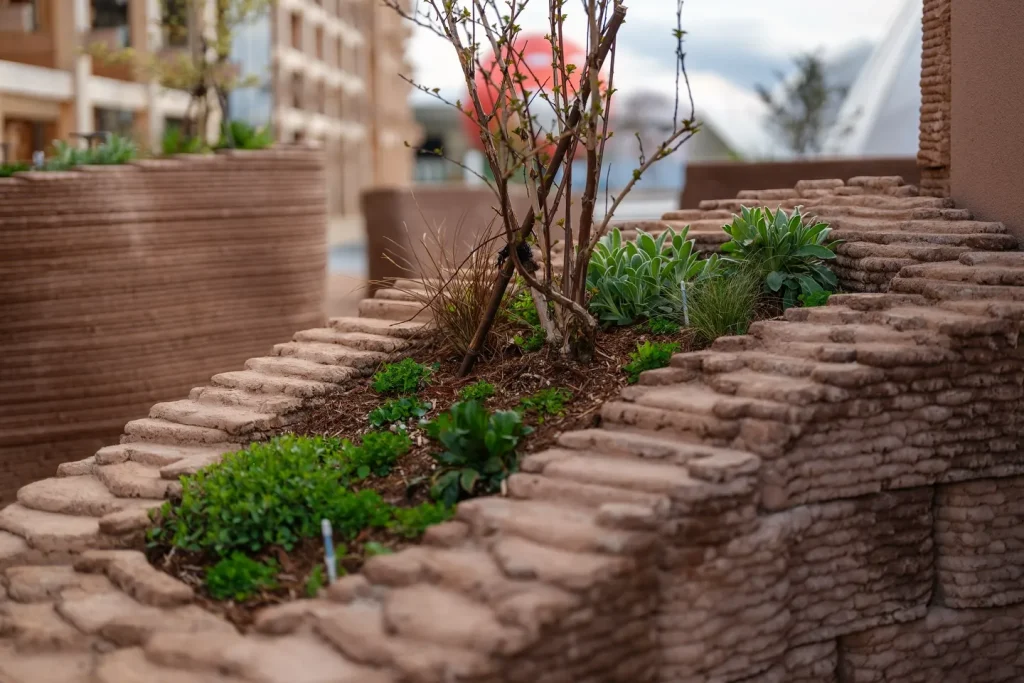
Some features, like planter-benches, were printed directly at the Expo site using the Crane WASP printer’s 6.2-meter diameter and 1.7-meter height build volume. Other components, like modular earthen blocks, were reinforced with bamboo rods, used as a biodegradable alternative to steel rebar, and filled with hardener to support stacked planters. Washbasins were printed off-site and fitted with concealed plumbing access panels, then installed beneath pre-cast countertops.
Aki Hamada Architects approached the project as a statement against the uniformity of industrial construction, proposing a more fluid model where materials are gathered from the site and complexity grows from time and labor rather than expense. “We wanted to present a glimpse of a future society in which humans, nature, and machines coexist,” said principal architect Aki Hamada.
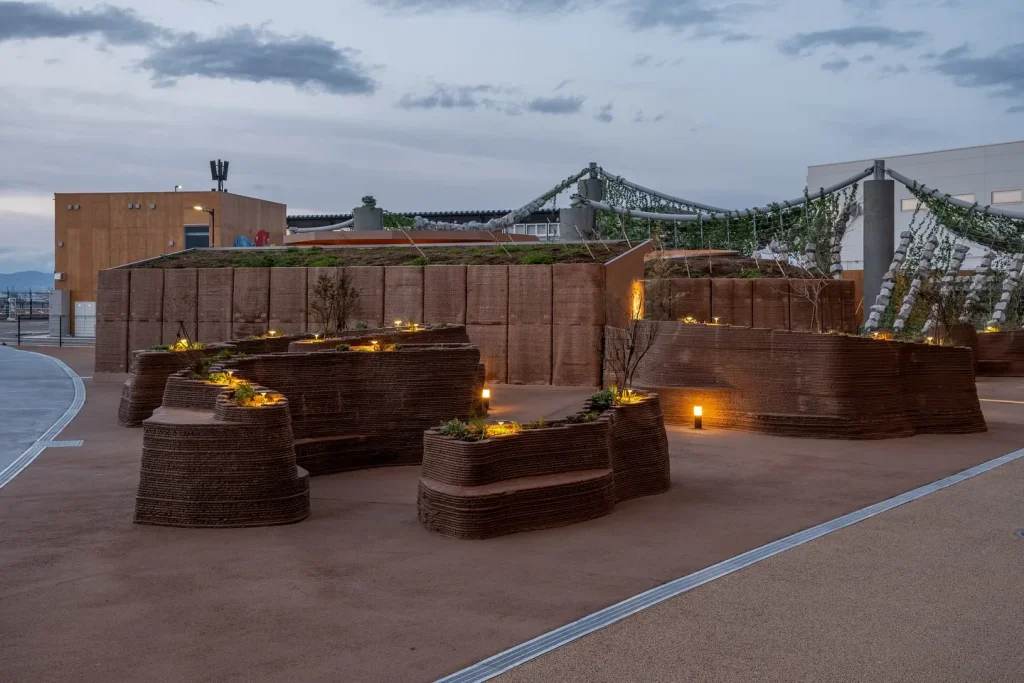
A Broader Movement
The project arrives as Japan and other regions in Asia and the Middle East increasingly explore the architectural potential of additive manufacturing. In early 2025, JR West partnered with Serendix to pilot a 3D-printed train station at Hatsushima Station, built in just six hours between nightly train operations. Meanwhile, Dubai’s Proto21 recently completed the world’s largest 3D printed architectural structure by volume, using over 21,000 custom-printed components.
Within this rapidly evolving landscape, Aki Hamada Architects’ earthen rest facility stands out for its material honesty and ecological logic. As Expo 2025 positions itself as a testbed for future societies, this project reminds us that innovation sometimes looks backward, to local soil, to slow processes, and to architecture that disappears as gently as it arrives.
Leave a comment