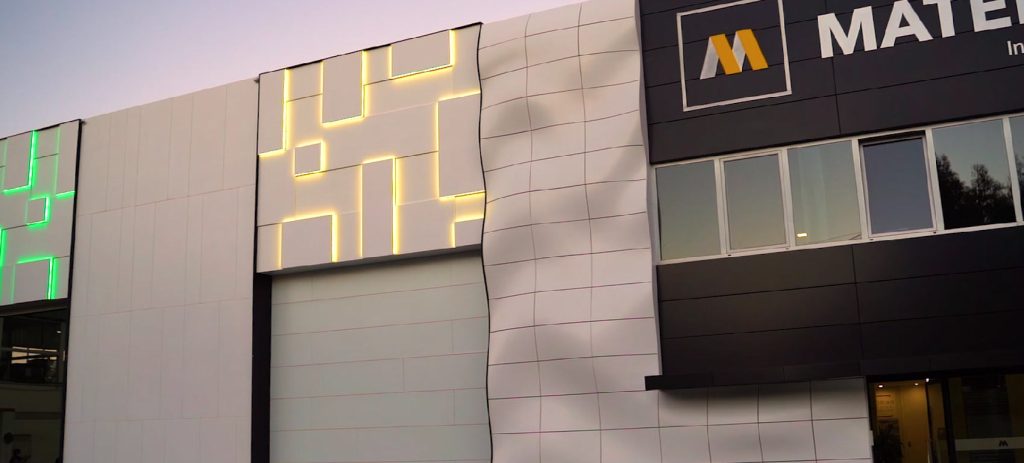
Corian® Solid Surface offers architects a sustainable and versatile material that seamlessly integrates with parametric design. Its 3D Fabrication Solutions, including Thermoforming and Automated 3D Fabrication, represent a revolutionary paradigm in sustainable architecture. Let’s look at Corian® Design’s efforts to develop innovative and sustainable 3D fabrication solutions.
To design parametrically has become synonymous with designing smart, environmentally friendly, and, most importantly, effective in terms of material waste and overall workflow. Such a design approach relies on advanced software and complex parameters and often leads to a completely futuristic aesthetic. To design parametrically is an all-encompassing endeavor across various professions involved in designing a structure: Architects are able to take various new importances – such as working sustainably from the design idea to manufacturing to construction – much deeper into account.
Engineers and manufacturers can share a 3D version of the intended design object, which can be much more delicate than standard Euclidean geometry, and construction workers involved in the erection of a building find themselves dealing with new materials, forms, and patterns yet often simple, logical and straightforward ways of installing these new high-tech elements. But one essential aspect is often taken for granted: For architects to be able to design buildings as vividly as computer programs can generate them, materials and construction techniques need to be on the same level. “New material technologies will be continually developed and enabled by parametric thinking.” writes Scott Overall in the book.
Corian® 3D Fabrication Solutions, Solid Surfaces, and new technologies
Corian® Solid Surface was developed by chemist Donald Slocum at the American chemical company DuPont® in 1967. Four years later, when introduced to the market and thanks to the material’s unique properties, it became obvious that this material spans beyond the architectural dimension and would become similarly of great interest to engineers, interior designers, and artists alike. However, as unique as this seems in retrospect, the invention of this material was no coincidence: The company DuPont®, founded by French-American chemist Éleuthère Irénée du Pont de Nemours in Delaware, has throughout its over 200 years of existence, repetitively advanced the field of material science: Neoprene, Teflon, Spandex, various synthetic leathers and nylon fabrics are only some of the inventions that reshaped fields of electronics, transportation, building and construction, healthcare, and workers safety henceforth.
Corian® Automated 3D Fabrication Solutions is a technology revolutionizing the building industry by responding to the latest technological changes in the design process. This innovative solution, which eliminates the need for wooden molds, represents a sustainable and environmentally friendly way of producing building materials. The solution reinforces Corian® Design’s leadership in Solid Surfaces by providing architects and designers with a fast, reliable, and cost-effective way of implementing Corian® Solid Surface exterior and interior cladding projects with complex geometries, curves, and irregular shapes. The solution also supports digital methods for optimization and computation of data in the design process, such as parametric design.
Advantages and properties of Corian® Solid Surface
One may better understand Corian® Solid Surface by asking one question: What do architects want? Architects may want to create a monolithic facade out of one material, in pleasant texture and various colors, with easy-to-install substructures and, above all, form it into organic shapes and curvatures based on various requirements. Corian® Solid Surface is exactly that. However, engineers might become more curious when hearing that the material has various benefits over other more traditional materials such as wood, concrete or metal: It is non-porous, resistant to UV and sun-fading, in the event of surface damage, despite its durability and resistance to dirt and stains, it can be easily repaired by cleaning and sanding.
With this information in mind, it is time to know what Corian® exactly is: On a chemical level, one can call it “[…] a material composed of one-third of transparent acrylic resin and two-thirds of natural minerals. The principal among these latter is alumina trihydrate, a white powder derived from bauxite, the mineral from which aluminum is extracted.” In other words: “It is a mineral material in powder form held together by an acrylic resin.” Initially in its development, as stated by Forbes, DuPont’s chemists (above all Donald Slocum) combined resins, epoxies, natural limestone, and pigments to offer a solid surface and thereby create an alternative to conventional kitchen countertops that often were made out of granite. It is a solid surface not only because a kitchen countertop could be made out of one block of Corian® Solid Surface but because if one were to cut through it, the inside of the cut would still be in that same color without any edges.
These possibilities and properties are becoming all the more relevant for the design industry when this material, Corian® Solid Surface, can be easily shaped along three dimensions while effectively preserving its final form without losing any of the just-mentioned benefits.
Previously, wooden molds have been used to create curved surfaces and 3D forms in fabrication. However, this method is known to be time-consuming and labor-intensive. Consequently, Corian®Design has developed a new method that eliminates most problems associated with wooden molds. Known as the Corian® Automated 3D Fabrication Solution, this unique technology is set to revolutionize design efficiency and sustainability. Furthermore, it is an adaptable technique that can be easily integrated into parametric design methods.
A recent advance in DuPont’s® manufacturing process has elevated this material to a realm of completely new possibilities: That process is called Thermoforming. When thermoforming Corian® Solid Surface, the panels are heated in an oven and then placed onto a reconfigurable mold. This mold directly adjusts based on the software setting, leaving no need to simplify any ideas. By using a reconfigurable mold (whereby many individual ‘presses’ can shape the panel in high detail and numerous ways), up to 40% of costs can be saved compared to conventional thermoforming methods (where for one form, one specific mold would need to be built).
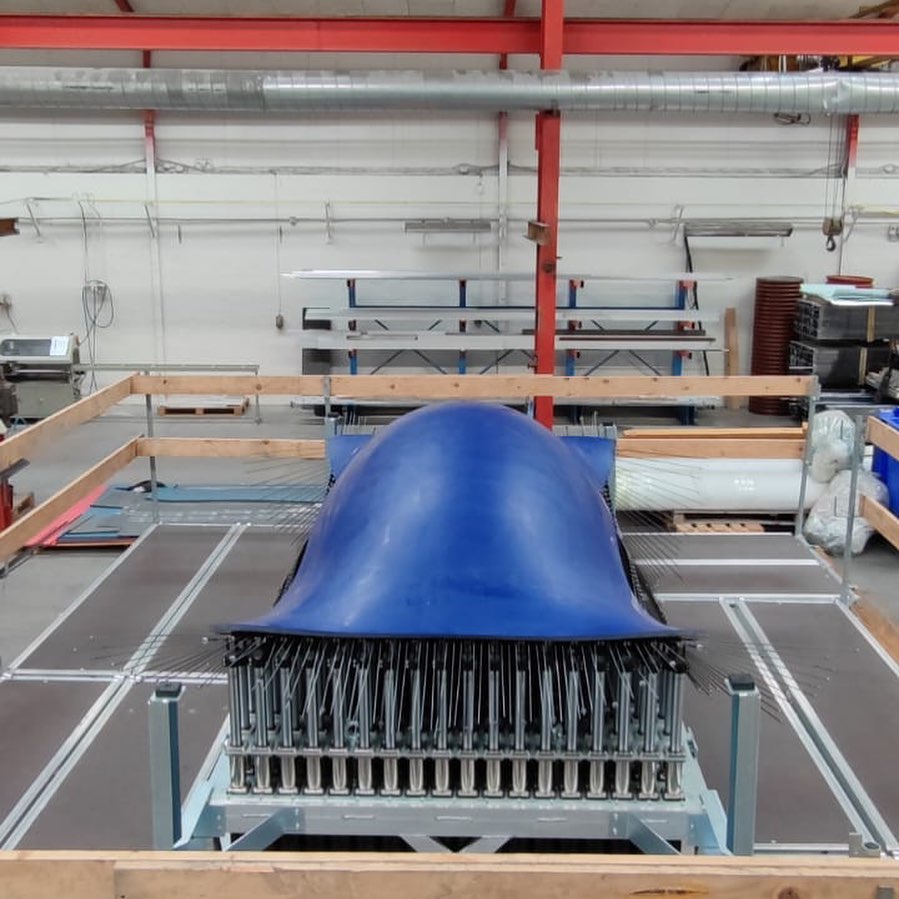
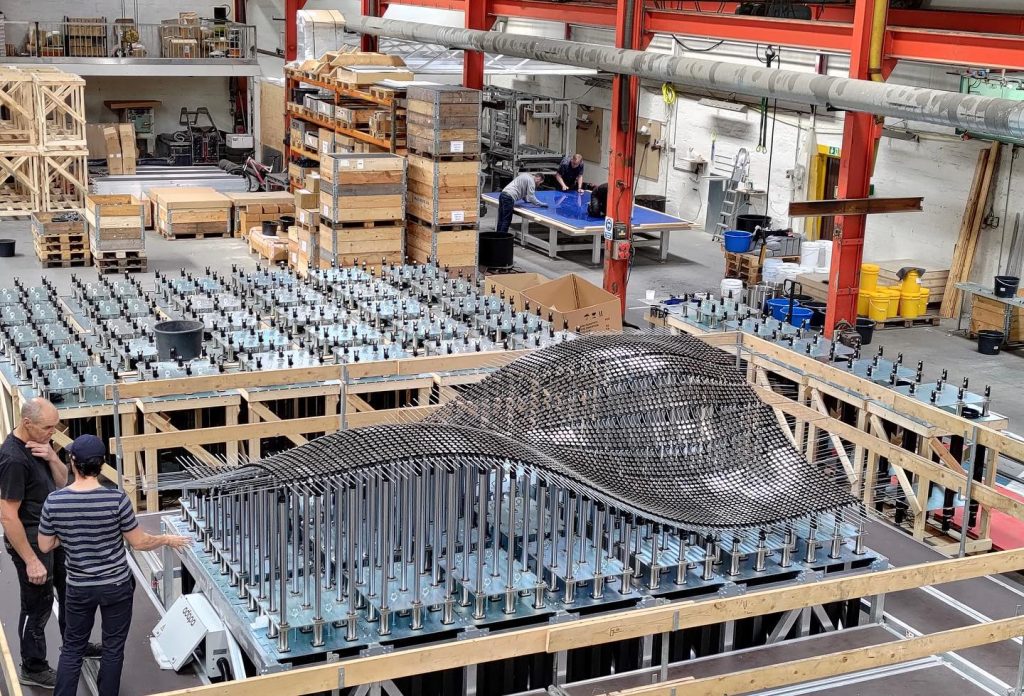
Costs are further reduced because no additional material goes to waste (as otherwise the case when molding and cutting conventionally). Through this intelligent process, the production becomes sustainable and resourceful. Once formed, the panel will be cooled, trimmed into transportable sizes, packaged, and delivered to the construction site. Corian® Solid Surface can take shapes that are summarized under the geometrical term Hyperbolic Paraboloids.
Here are the advantages of Corian® Solid Surface with 3D panels in architectural projects:
- Corian® Solid Surface integrates with digital design tools for efficient optimization and data computation, streamlining the transition from 3D drawings to complex-shaped panels.
- The use of 3D panels allows for expedited Corian® project completion, achieving speeds up to 10 times faster.
- Implementation costs are significantly reduced, up to 40%, due to the cost-effectiveness of fabricating and installing 3D panels.
- The production process of Corian® with 3D panels promotes sustainability by eliminating the need for wooden molds, contributing to environmental conservation, and saving over 100kg/m² of wood.
From factory to building
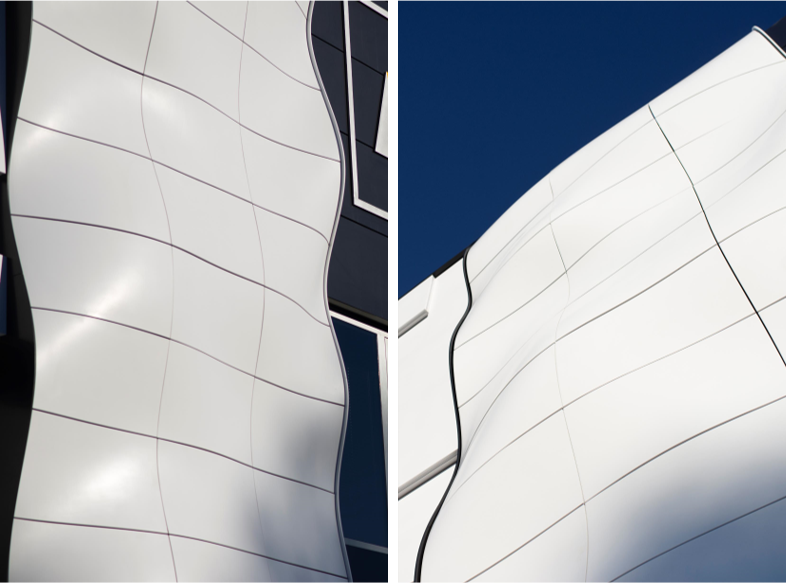
Cláudia Martins Costa, Marketing Coordinator at Materfut®, a company specializing in importing and handling innovative materials and one of the first to use Corian’s® Solid Surface 3D-fabricated (thermoformed) panels on the facade, states: “The finished facade looks exactly, like the initial design, we were not forced to simplify shapes and geometries of the cladding panels.” In the case of the Materfut® headquarters south of Porto, only 10 curved panels were needed to design the facade. Over 60 panels would have been needed to build this facade using conventional panels. In fact, for the 35m² Materfut® facade cladding, using Corian® Solid Surface saves around 100kg wood per m² (for the mold) whilst also being ten times faster and therefore, significantly more cost-effective.
Additionally, through good packaging, workers will have no struggle installing each panel in its right spot. Moreover, the three-dimensional Corian® Solid Surface panels have small visible joints (or gaps between them) compared to conventional facade elements, giving the facade a clearer, simpler and more elegant look. Having panels of such intricate forms, DuPont’s® ability to produce them can be understood as material expression of parametric design, in which highly flexible materials accommodate changing parameters in aspiration of designing new aesthetics, meeting criteria of sustainability and flexibility by imitating nature in its complexity.
By using the three-dimensional Corian® Solid Surface panels as facade cladding, the facade becomes visually stimulating for the eye and reflects light differently depending on the daytime. In the interior, the panels show other qualities, and their versatility becomes clear for different reasons. Linea Pannelli®, a distributor of Corian® Solid Surface in Northern Italy, has created a fascinating wall to help designers explore parametric design visually and haptically through the creation of walls using Corian® Solid Surface.
The company has installed an eight-metre-long and two-and-a-half-metre-high wall. Half of this wall is made of one large panel with different curvatures in the Glacier White color, including an oak-wood black bookcase. The other half is a composition of smaller panels with open joints in the colour Artista Dust. On this half, one panel is backlit with LED’s for a smooth ambient light. Gianluca Reginato, Sales Manager of Linea Pannelli, explains: “This wall is an abstract and conceptual style exercise. It was designed to offer a visual and tactile experience of the potential of Corian® Solid Surface in vertical applications […].” Using the material in the interior, the panels show their variety – one can envision a cosy wall at home in the color of Artista Beige up to a clean exhibition space in various shades of white.
Case studies: When designers handle Corian®
The 3D-facade elements are Corian®Design newest production method and state-of-the-art when handling Corian® Solid Surface. It is now up to architects, engineers, and designers to utilize the new potential and determine its aesthetic use. However, as stated in the beginning, the material and its silky surface have attracted famous designers and architects for a long time. In 2007, for example, French architect Jean Nouvel used it for a scenographic exhibition in Milan, Italy, titled Corian Nouvel Lumiéres.
In this exhibition, Nouvel emphasized the translucent and atmospheric nature of the material, stating: “I decided to evoke atmospheres linked to the different components of the house: kitchen, living room, dining room […]”. Similarly, Zaha Hadid, herself a pioneer of parametric design experimented with Corian® Solid Surface in her design of the Z.Island Kitchen for Italian kitchen design studio Ernestomeda: “The futuristic Z. Island project is a ‘smart’ environment that meets a number of functional demands made on kitchens, both conventional [washing] and innovative [music].” This kitchen is a beautiful take on the material, not only because it references the origins of Corian® Solid Surface (as a kitchen countertops), but shows similarly that a material can be functional yet elegant and progressive alike.
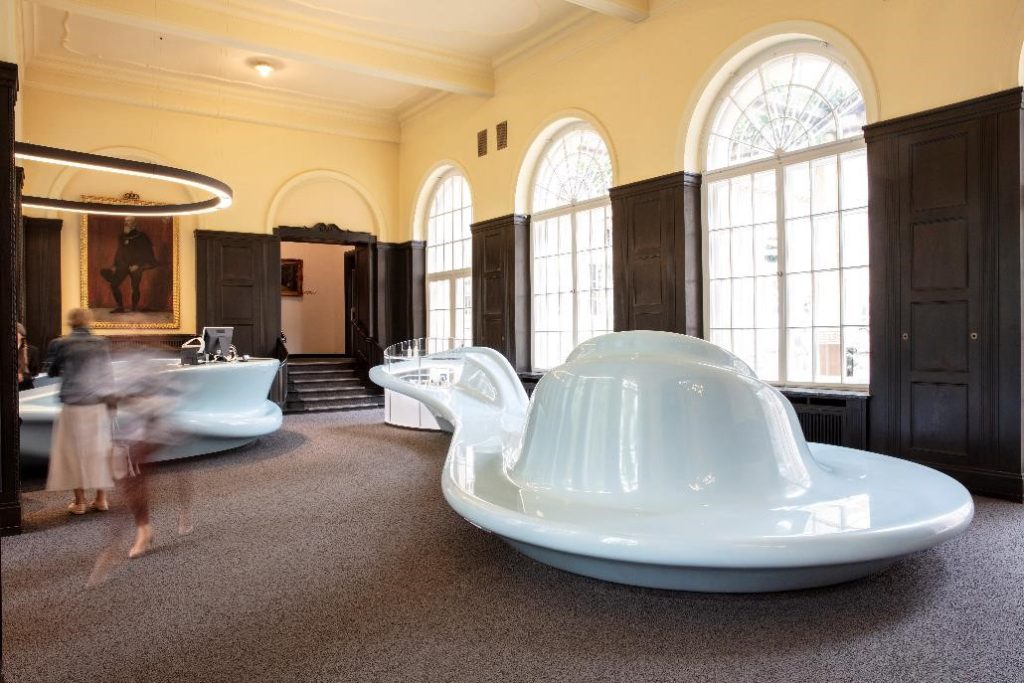
There are numerous case studies and a wide range of applications for Corian® Solid Surface. Two of them are the interior ‘counters’ of the tourist information in Bad Kissingen, Germany, designed by German office architect. “However, the word “counter” is reductive: these furnishing elements develop like waves through the space […], providing an ideal display […] for information material, a seating solution and reading area, as well as a practical shelf and writing surface.” Here, the characteristics of the material are used to accentuate and define a rather small space in an elegant way yet to also form a contrast between other wooden and more historic decorative elements.
Further fascinating is the application by Axel Schoenert Architects (ASA), which has renovated an office compound consisting of three buildings located at 54 rue de Londres in Paris. The facade is gracefully structured with Corian® Solid Surface panels – here using 2D-elements – but one can easily imagine that the new three-dimensional thermoforming technology could have added yet another beautiful dimension to this facade, making it even more vivid and sculptural.
Working with Corian® Solid Surface
Corian® Solid Surface is no longer a patented material but must be sold and installed by a DuPont® certified fabricator. However, it is sold by manufacturers all around the globe – from the United States to Argentina, Europe, the Middle East, Africa, and throughout Asia. To find a distributor, visit the local or national Corian® website in your country or have a look here. Through this form, contact to a DuPont®-office or sales representative can be established, samples can be ordered and more generally, local distributors can be found.
Leave a comment