This study focuses on using 3D printing of cement-free mineral foams made from recycled materials to build solid, light, and insulated walls. Its goal is to use moldless fabrication through large-scale robotic 3D printing to reduce the amount of material, labor, and costs needed for custom-making parts. Using porous materials with different densities can help with insulation and power where it’s needed, which can lower the amount of energy needed to heat buildings.
Building parts that are made of only one material with different thicknesses can be reused and recycled in the future. FenX’s cement-free mineral foams also leave less of a carbon footprint than foamed concrete or plastic foams. The automatic 3D printing system is being made at ETH Zürich with help from FenX AG.
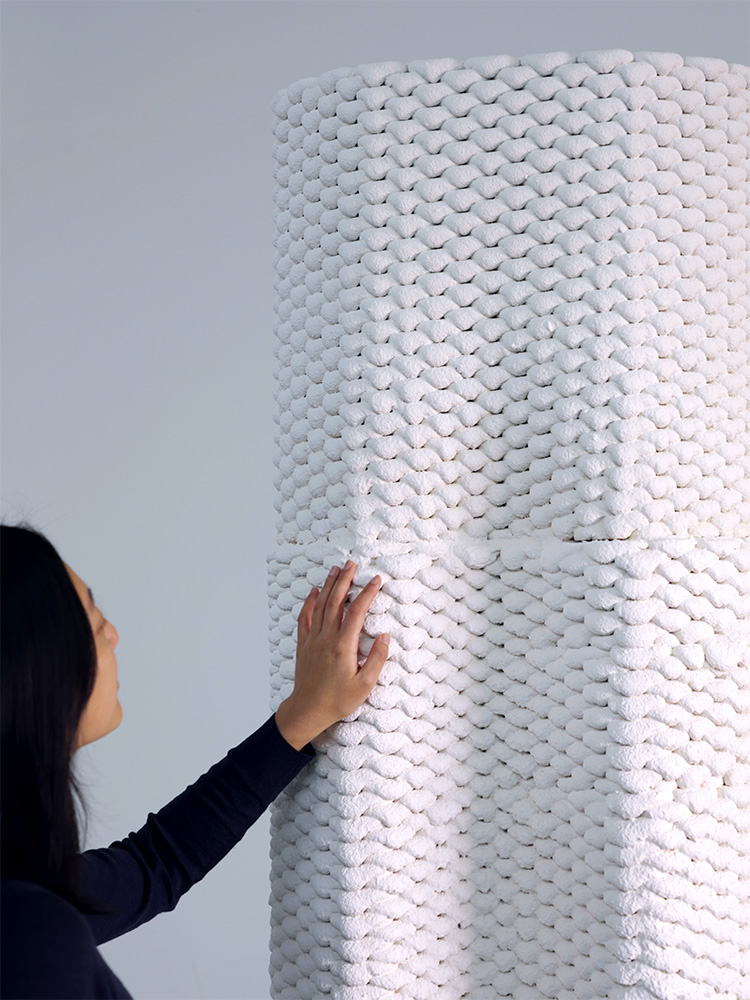
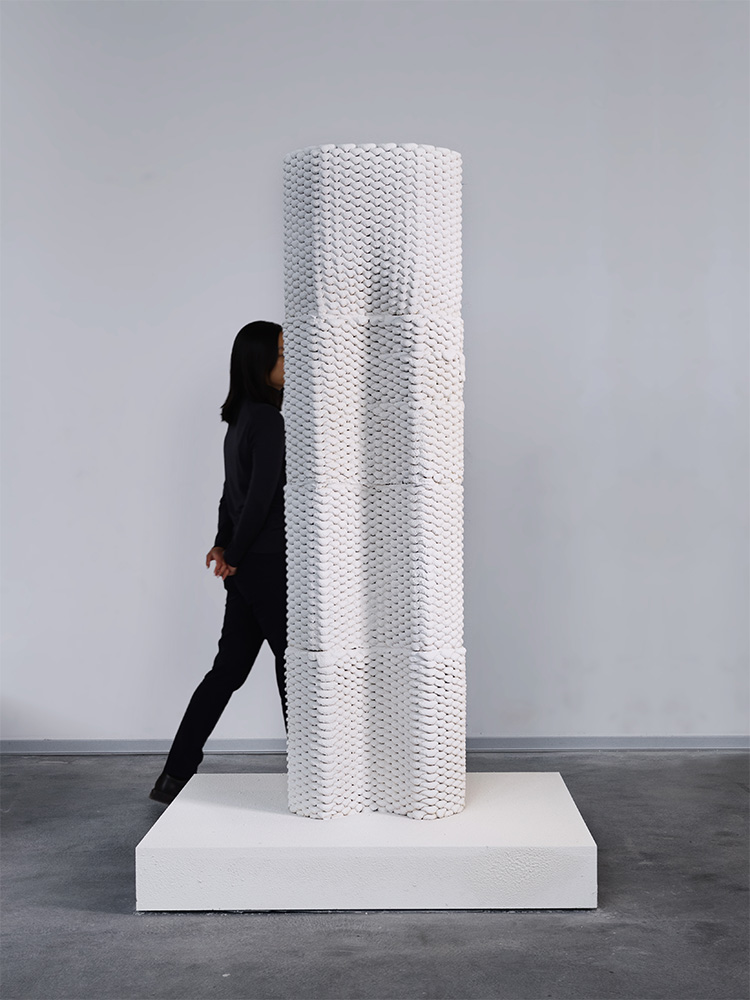
Airlements is the biggest prototype that came up in this study. It is made up of four 3D-printed parts and stands 2 meters tall. All of the parts were 3D-printed in less than an hour and then hardened for a week in a controlled setting that kept the temperature between 20°C and 28°C and the humidity between 20 and 70%. Because of this, processing that uses a lot of energy is not needed, which is an improvement over earlier research that used cement-free mineral foams. The curved texture of the prints comes from the way the paths are set up, which makes the material stronger while it hardens and when it’s finished.
Each of the four hollow parts is only 25 kg, so one person can move them. The hollow core can be filled with mineral foam to make a single unit, and a cover of cement-free plaster can be used to protect it. This method can be used for non-structural exterior walls. Casting can also include reinforcement and infrastructure improvements, which could make it more useful in more situations. In the future, the 3D printing system will be improved by making the parts more precise and raising their load-bearing capacity. The Airlements prototype is a big step forward in studying digital manufacturing with foamed materials.
Project Info
Team DBT: Patrick Bedarf, Anna, Szabo, Prof. Benjamin Dillenburger
Team FenX: Alex Heusi, Aybige, Öztüre, Lex Reiter, Enrico Scoccimarro, Michele Zanini, Etienne Jeoffroy
Technical Support: Tobias Hartmann, Cilgia Salzgeber, Jonathan Leu, Lucas Petrus, Philippe Fleischmann, Michael Lyrenmann, Heinz Richner, Bharath Seshadri, Angela Yoo
Photography: Hyuk Sung Kwon, Patrick Bedarf | dbt
Leave a comment