Self-assembling timber shells known as FLIM-FLAMS (Force-Lifted, Timber, Flat-Laminated Shells), designed by i/thee & Neal Lucas Hitch, are produced by radially cutting patterns from flat sheet materials, which are then laminated together and stretched upward to form quickly deployable wooden tents.
The procedure simulates the deformation of flat geometries cut with computationally optimized radial patterns upon being lifted from a central axis by means of sophisticated digital software. Then the flat radial pattern is cut onto readily available plywood panels, turning flat sheet goods into enormous wooden springs that become doubly curved, bending-active vaults when raised from their center.
The FLIM-FLAMS procedure was created at Cornell University’s Department of Design Technology and built in collaboration with The Soil Factory, an Ithaca, New York non-profit that promotes innovative sustainable practices. It has historically been challenging to accomplish complicated bending with timber components without generating a considerable amount of material waste since wood cannot be easily molded or cast like other common building materials like steel, plastic, or concrete.
On the other hand, FLAM-FLAMS employs a novel method that uses computational tools to support hand-building processes in order to create intricate timber shells that are flat-fabricated, quickly deployable, and waste-free.
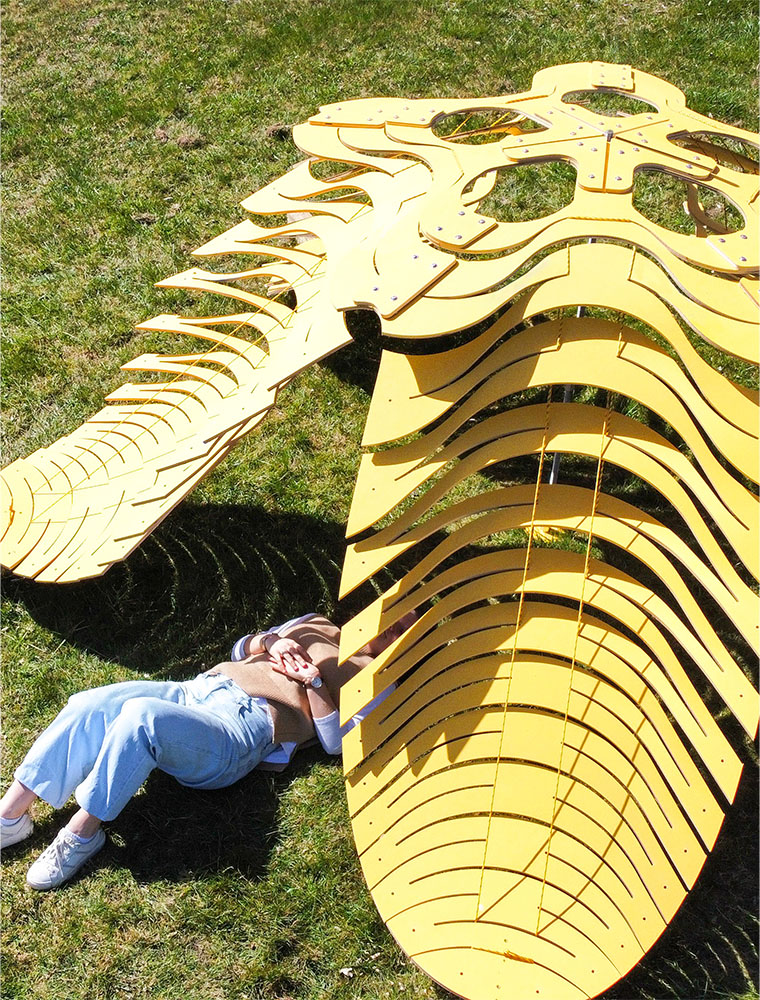
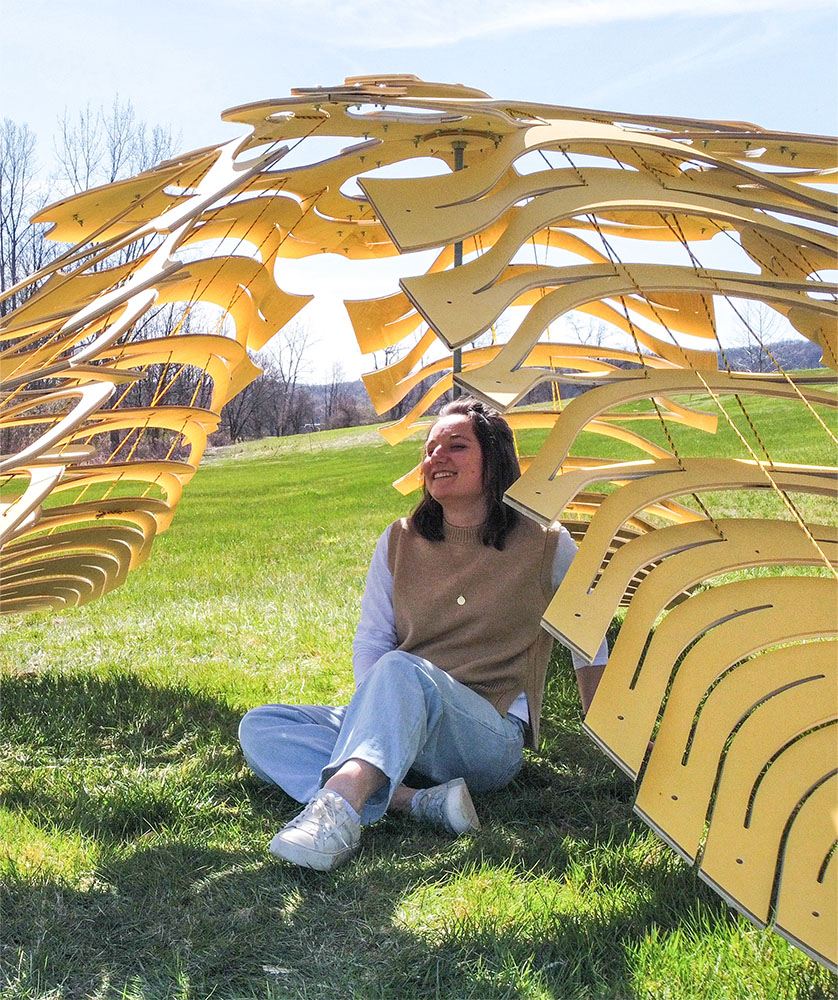
Digital Design and Preparation
The process of creating FLIM-FLAMS digitally begins with a computational approach that codes radial patterns that are undulating and sliced into flat shapes using biological principles. Then, in order to replicate the self-assembly process, these geometries are virtually replicated. Using a two-axis CNC mill, the digitally optimized cut design is first etched into flat plywood sheets to begin the physical manufacturing of FLIM-FLAMS.
After that, the sheets are delivered to the location and laminated at the short ends to form a single, sizable, flat sheet with a 15-foot diameter. Ultimately, a 60-inch-tall hexagonal nut beneath the plywood is threaded up a central rod. The plywood eventually self-assembles into its final vaulted shape when the nut is raised.
The ultimate result is a technique for building with wood that changes wood, which is typically chosen for its stiff qualities, into a flexible membrane with the ability to bend complicated shapes quickly and easily. This project shows how wood may be used to create multi-curving geometries without requiring the large amounts of material waste that are usually involved with CNC cutting curved wood components.
Furthermore, the project serves as an example of how technological and analog procedures might combine to produce more sustainable design solutions by fusing modern digital processes with traditional physical construction approaches.
Project Info
Project Name: FLIM-FLAMS (Force-Lifted, Timber, Flat-Laminated Shells)
Office Name: i/thee & Neal Lucas Hitch
Lead Architects: Neal Lucas Hitch
Completion Year: 2024
Gross Built Area (m2/ ft2): 200 ft2
Project Location: Ithaca, New York
Photo Credits: Thanut “Hint” Sakdanaraseth
Leave a comment