Facade cladding refers to the process of covering the exterior surfaces of buildings with various materials. Facade cladding, which protects the body part of the external walls from environmental factors and helps the space to provide suitable conditions in terms of building physics and user comfort, also increases the aesthetic value of the building.
Facade cladding is an element that develops the personality and character of a building. When selected properly, cladding materials provide exterior protection, ventilation, insulation, energy efficiency, and structural durability. Facade cladding, which is a way for the building to integrate with the environment and affects the perception received from the building, can vary depending on the geographical region, use, climate, design, and budget.
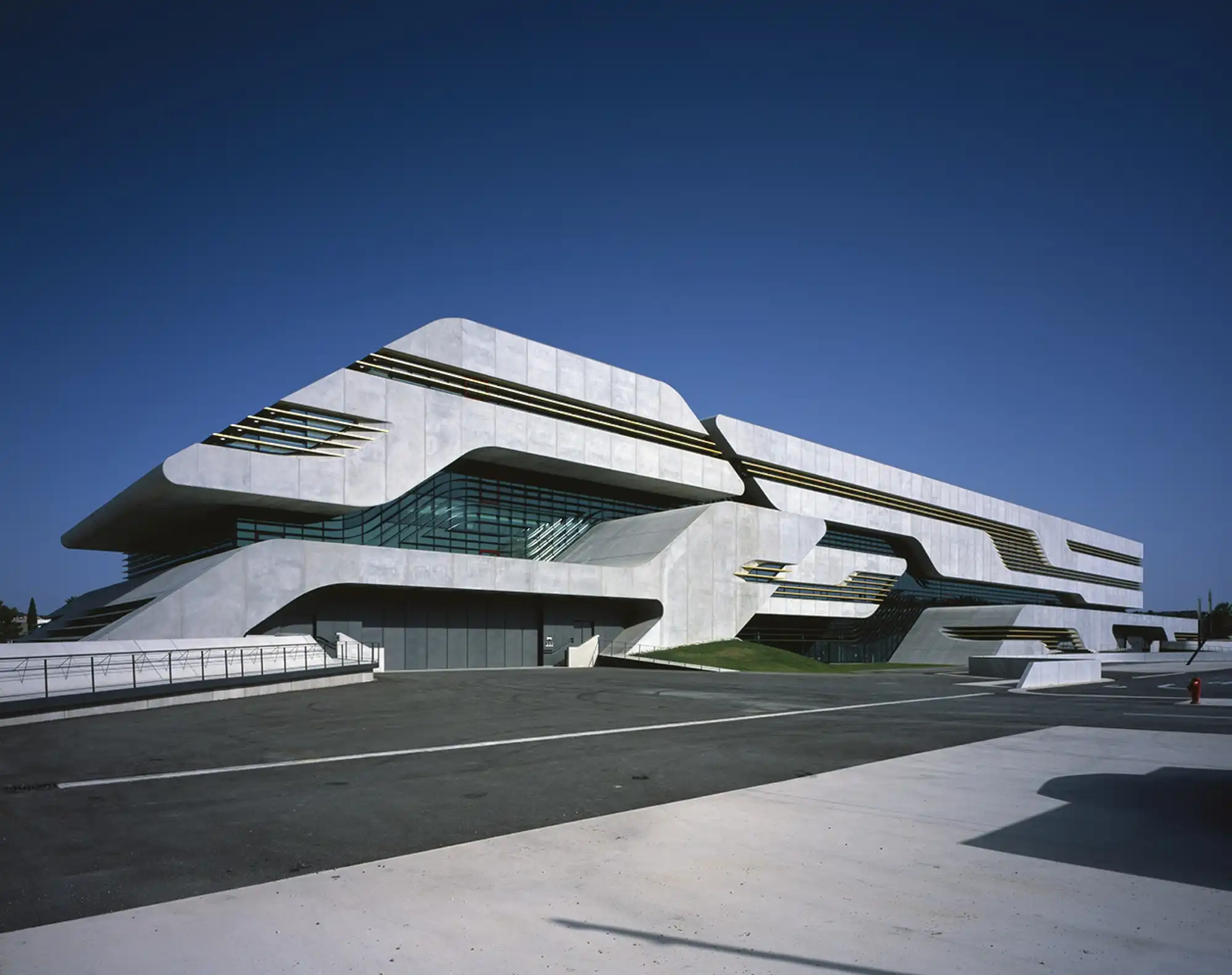
While the materials covered on the external walls of buildings are expected to have features that are suitable for the building design and increase the aesthetics of the building, they are also required to be resistant to environmental conditions such as wind, sun, and rain. The façade coatings, which must support heat, water, moisture, sound, and air insulation, are easy to maintain and repair, and are easy to clean, which are features that make the material preferable. The external wall body preferred in the building design is important for the selection of façade coating. We can list the external walls as follows:
- Stone Wall: Commonly used as a structural element in historical buildings, stone walls are highly durable against external factors.
- Brick Wall: Brick exterior walls, which are formed by laying bricks with mortar and are frequently preferred in traditional houses, have advantages such as low cost and easy workmanship.
- Reinforced Concrete Walls: Often used as load-bearing elements in modern structures, these walls combine steel reinforcement with concrete to provide high strength.
- Autoclaved Aerated Concrete (AAC) Wall: Aerated concrete, which allows for a very light exterior wall construction, also provides good insulation.
- Timber Frame Wall: Found in buildings that use a wooden frame system.
- Steel Frame Wall: It is a frame system formed by the combination of steel profiles that provide the carrier capacity of the structure.
The facade cladding that gives the first impression of a building should be selected according to the external wall of the building and should be applied with the most appropriate installation method. Here are 10 facade cladding materials preferred for cladding buildings with both visual richness and functional advantages:
Exterior Plaster Coatings and Paints
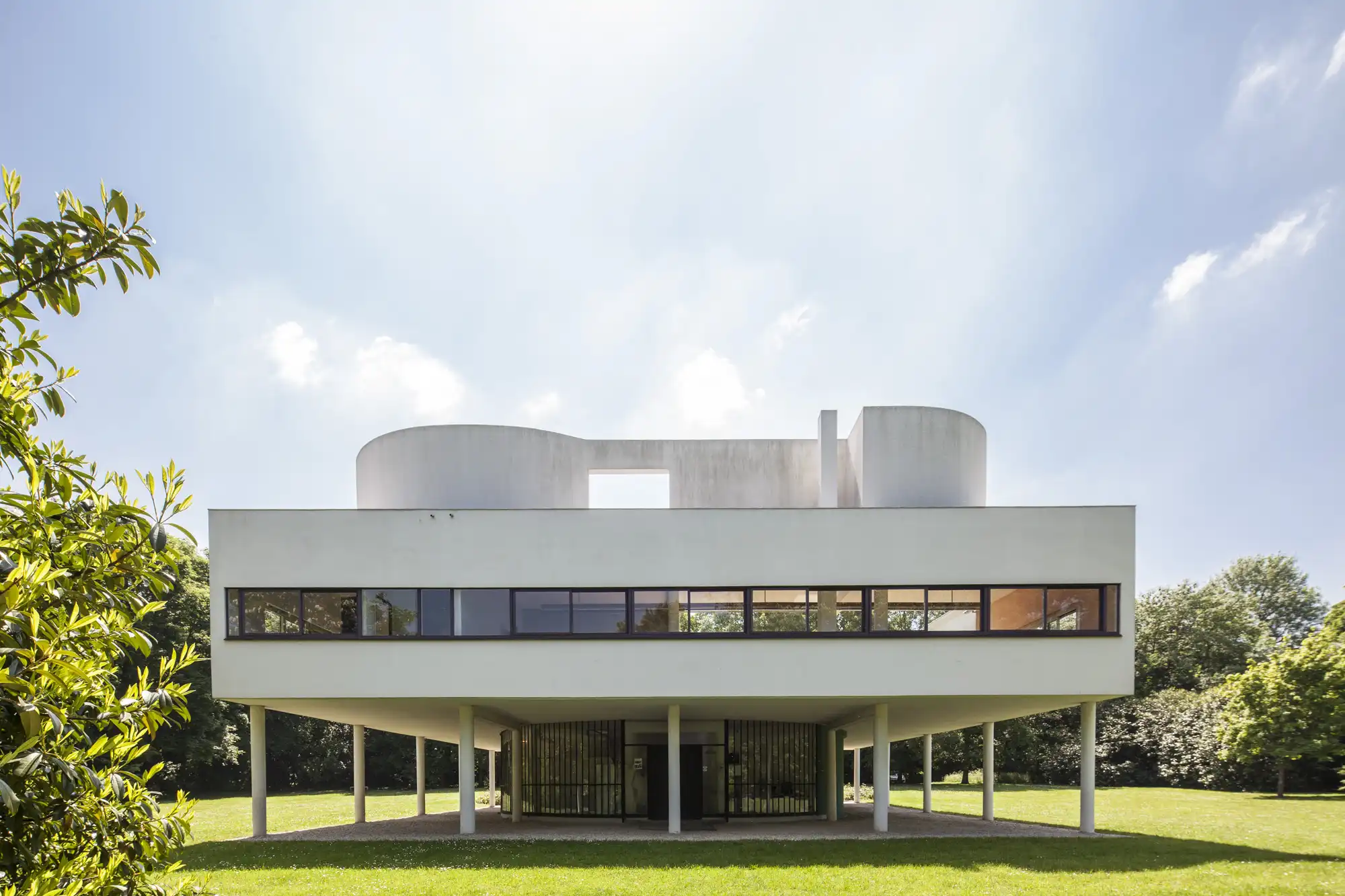
In the external plaster coating applied to the external surface of the structures, binding materials such as cement, lime, and plaster are made by mixing sand and water and applied to the wall body while it is in a plastic consistency. The external plaster coating, which provides a homogeneous appearance to the surface while protecting the structure from external factors, can be finished with paint or decorative coating after application.
Plasters, which protect the surface against rain, snow, sun, and pollutants while closing micro cracks and preventing water from leaking into the structure, usually consist of two layers as rough plaster and fine plaster. In traditional plasters, rough plaster is 15-25 mm, and fine plaster is 5-10 mm, while primer is applied between the two plasters when necessary.
Factory-produced ready-mix plasters—dilutable with water and enriched with fillers, aggregates, and pigments—can create smooth, textured, or colored surfaces. These plasters are applied in varying thicknesses, generally between 2–4 mm. Depending on the method of application, buildings can achieve different patterned appearances. Ready-mix plasters can be classified by their binder types as follows:
- Mineral Plaster: Made by using granulated natural marble particles as a binding additive, mineral plaster can also be created by mixing colorized, ceramic-coated sand using a special method.
- Terrazzo Plaster (Terasit): Terrazzo plaster can be colored as desired. It is resistant to weather conditions, has low water permeability, and offers long-term durability.
- Acrylic-Based Exterior Paints: Acrylic-based, known as standard exterior paints, are resistant to sunlight and climate conditions. They are often preferred on surfaces such as concrete and brick.
- Silicone-Based Exterior Paints: Silicone-based exterior paints, which have water-repellent properties due to the silicone they contain, are resistant to climate conditions and long-lasting.
How to Apply Exterior Plaster?
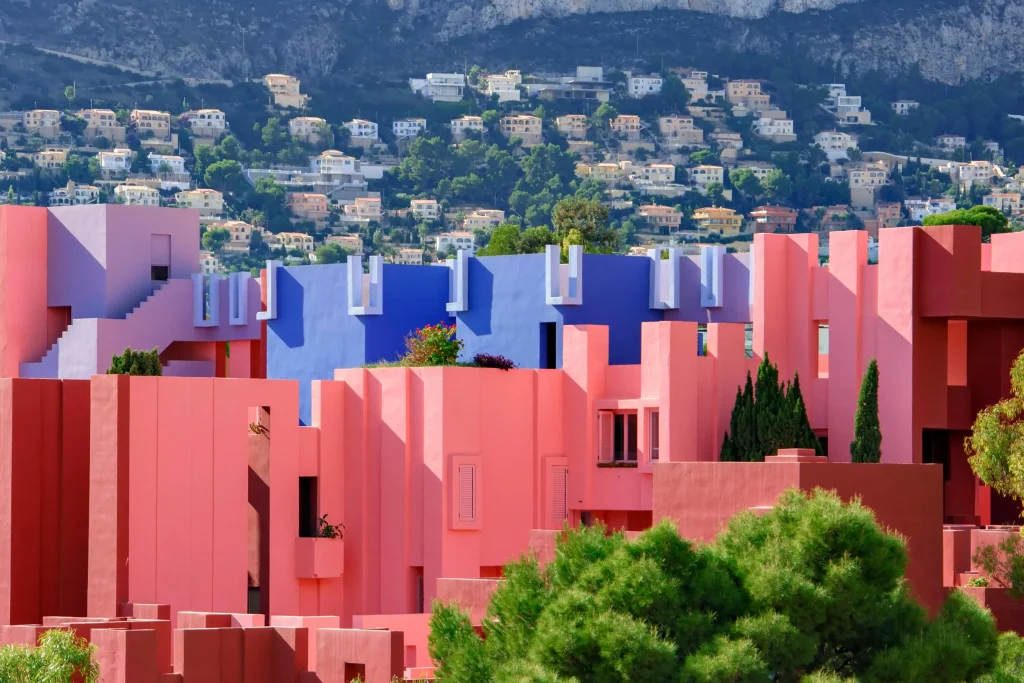
Before starting the exterior plaster application, the outer wall surface should be inspected for any issues and prepared accordingly. The application surface must be dry and solid. After selecting the appropriate thermal insulation material, the thermal insulation detection on the wall surface should be completed. Once the insulation boards are adhered, doweling is performed at least 24 hours later using a drill.
Following the doweling process, the first layer of plaster is applied, reinforced with a high-tensile-strength plaster mesh. Then, the second layer of plaster is applied. In the final layer of plaster application, texture can be given to the surface with traditional trowel plasters, brush, or sponge, optionally. After the plastering is completed, the surface must be protected from rain, frost, and excessive sunlight for 24–48 hours.
Exterior plaster coatings, which offer a wide variety of material and texture options and provide waterproofing, help to conceal imperfections on the wall surface and are easy to repair. Plasters selected as the facade coating of many buildings, from residences to commercial structures such as schools, hospitals, and offices, are also used in historical building restorations.
Wooden Facade Cladding
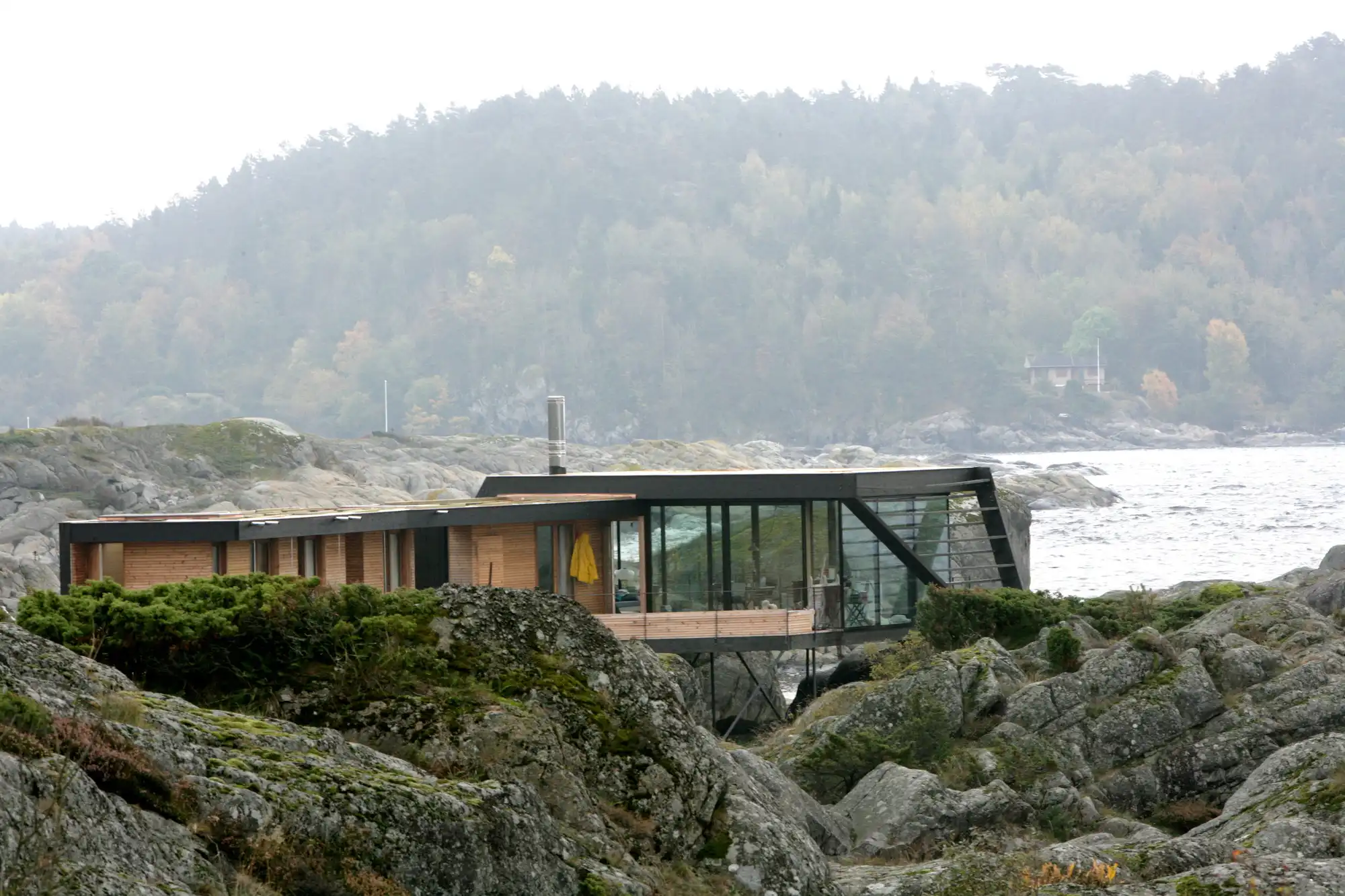
Wood, which is an indispensable source of raw materials for all living spaces, is frequently preferred as an exterior wall cladding material. As a natural material obtained from trees, wood requires less energy for production and use compared to other materials. Wood, which is a lightweight cladding material, is earthquake-resistant and can be given heat insulation properties thanks to special materials added to it. Due to its breathable nature, condensation does not occur on the surface, and wood cladding can be used in harmony with other materials. However, when used with materials that have a high moisture content, the surface may crack.
Wood, which can be used directly as it is produced, can also gain a different dimension with different designs by aging, burning, and staining methods. As an exterior cladding, wood offers a wide range of design options and versatility, making it a sustainable material and an environmentally friendly choice for exterior facades. Various types of wood are preferred for exterior cladding, each with its own unique properties and appearance. These are:
- Cedar: Cedar, which has a natural resistance to rot and insects, combines durability and natural beauty.
- Red Pine: Offers high durability and resistance to moisture.
- Pine: Offering a wide range of cladding, pine is also an affordable option.
- Oak: Known for its strength and durability, oak adds elegance to buildings.
- Spruce: This light-colored wood has medium durability and is economical.
- Iroko/Teak: A type of wood in the tropical group is known for its very high durability.
- Thermo Wood: Thermo wood, which consists of pine strengthened with heat treatment, provides high durability.
How to Apply Wooden Facade Cladding?
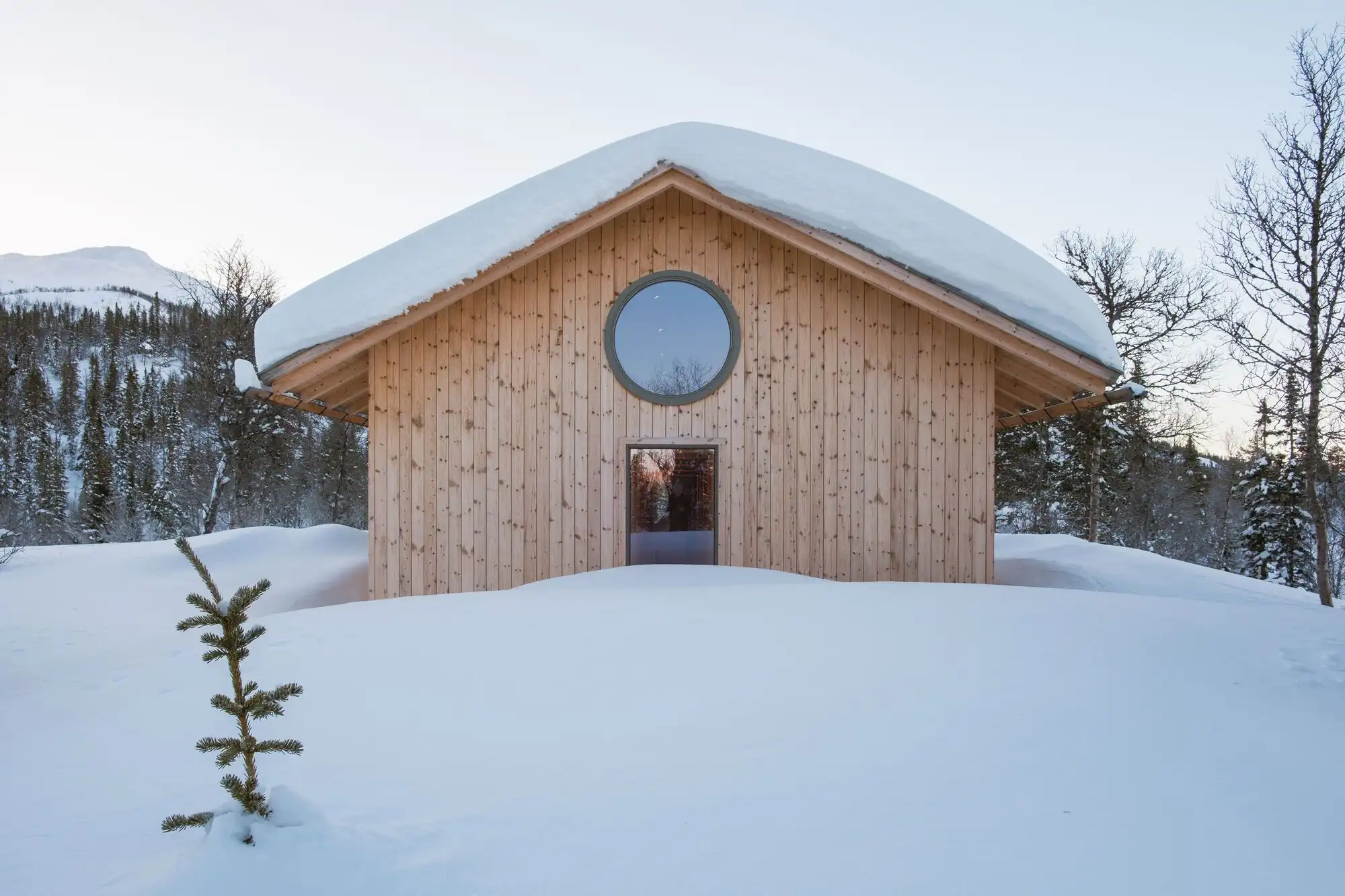
Wood must undergo some checks before being processed. Its moisture content should be below 12%, and it must be treated against mold, insects, and decay. After sanding, the wood achieves a smooth and uniform appearance, making it ready for cladding on the facade. The coating can be applied after the exterior wall surface is also ready for coating.
Wood cannot be mounted directly onto the wall; a substructure must be created first. A gap of 2-4 cm is left from the wall, and thus, air circulation is provided behind the wood. Wood facade cladding is preferably mounted on the wall with wood or galvanized steel profiles. Special interlocking methods can be used to create hidden connections, making screws invisible.
Additionally, wood can be used as a cladding material with special facade adhesives, particularly for horizontal cladding. Correct installation techniques are crucial for ensuring the longevity and performance of wooden exterior cladding. The installation process includes providing adequate ventilation, allowing for expansion and contraction, and using appropriate fasteners and sealants.
Natural Stone Facade Cladding
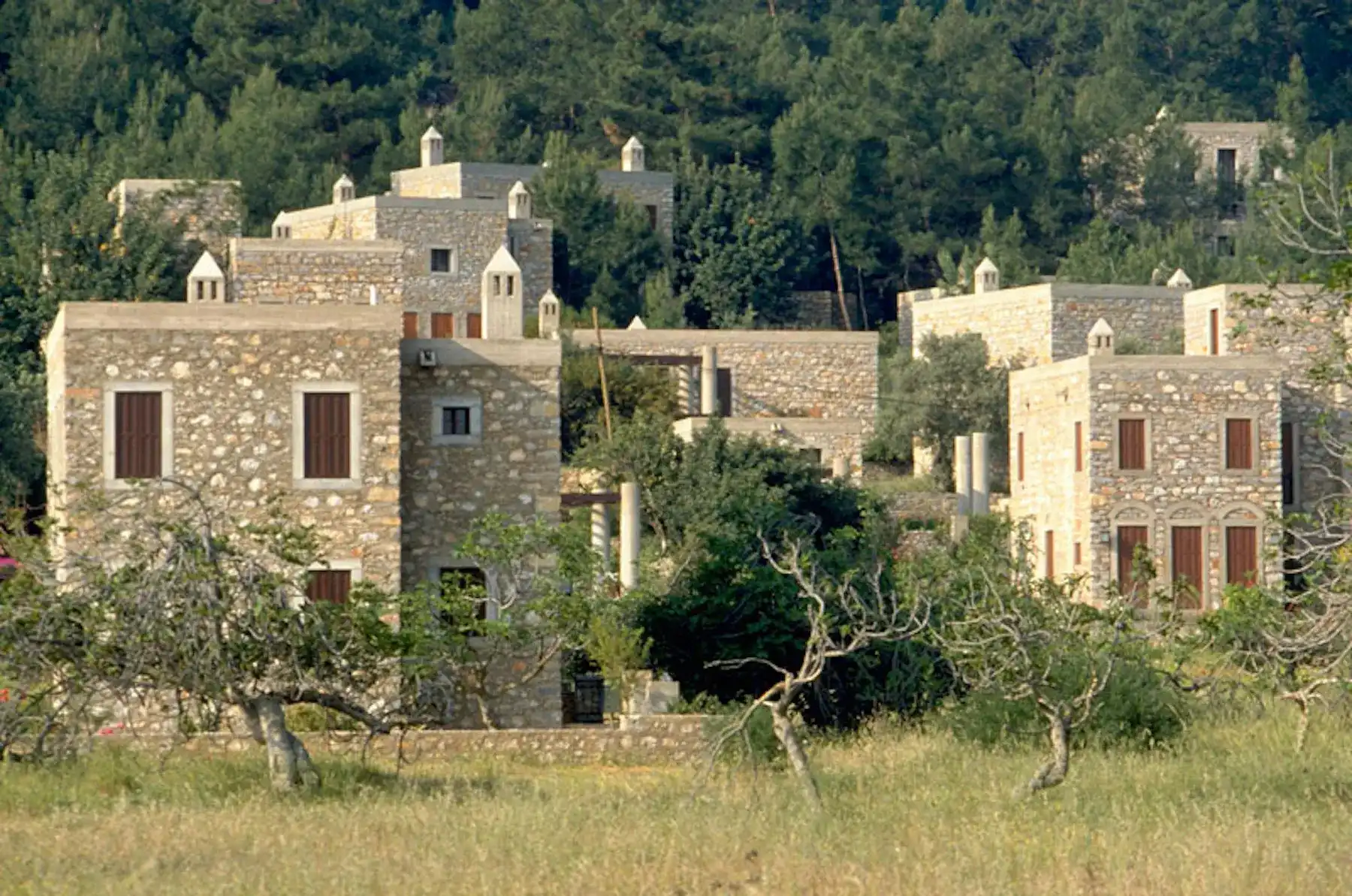
Natural stone, which has been a fundamental building material for living spaces for centuries, is frequently preferred for exterior facades due to its aesthetic appeal. Each stone block is unique, and thus natural stone-clad facades gain their own characteristic features. Natural stone systems, which offer both aesthetic appeal and long-term durability to designs, include natural forms of stones or specially cut and arranged stones. Natural stones with different stone types, colors, and textures provide creative originality for designers.
In addition to their aesthetic appeal and resistance to weather conditions, wear, and impact, natural stone facades are also favored because they require minimal maintenance and are an environmentally friendly material. Natural stones, which are slightly more expensive than other types of cladding, vary in cost depending on the material used, coating thickness, and workmanship. The types of natural stone used in exterior cladding are as follows:
- Granite Coating: Granite, a durable and hard material, offers a long-lasting and aesthetic structure.
- Limestone Coating: Limestone, which can be used in interior and exterior coatings, offers a natural and rustic atmosphere.
- Schist Coating: Durable and high-density schist is suitable for exterior walls, terraces, and drainage systems.
- Basalt: Basalt, of volcanic origin, is a durable and low-water-absorbing material.
How to Apply Natural Stone Facade Cladding?
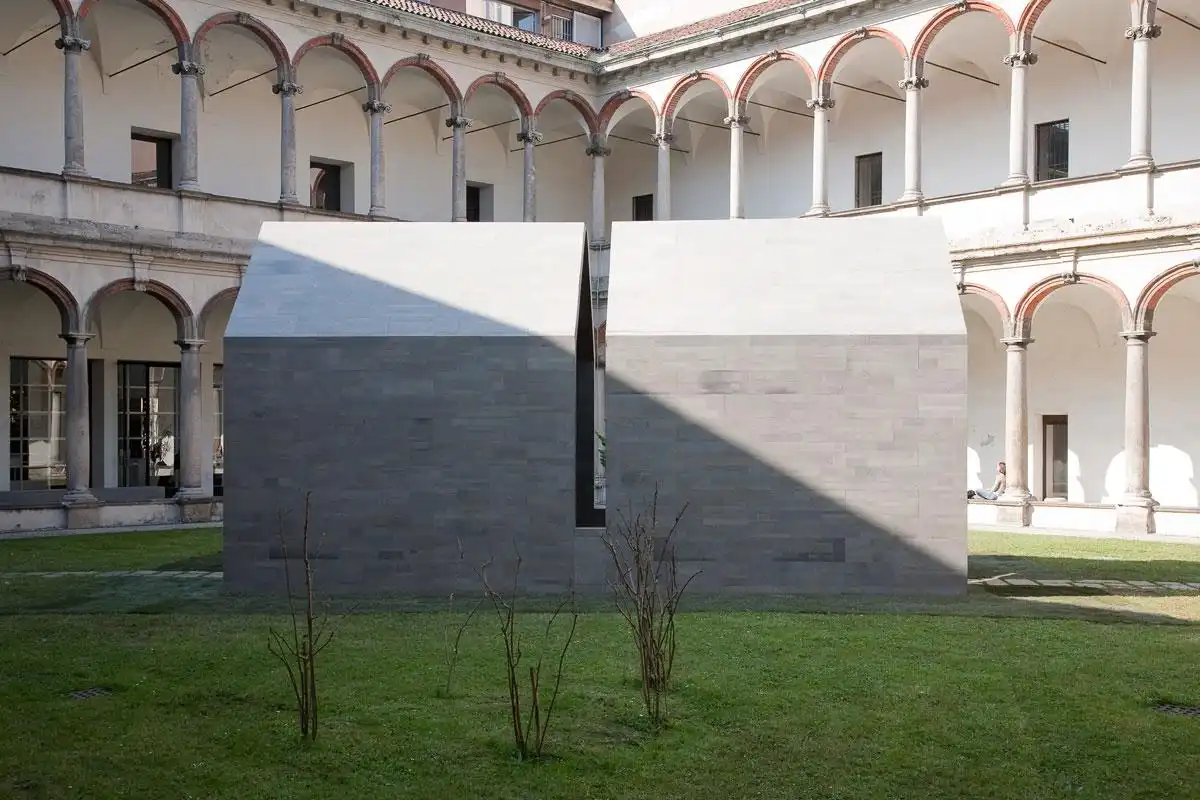
In natural stone coating, which requires meticulous work, the surface to be coated must first be prepared for coating. The adhesive suitable for the selected natural stone must be chosen based on the project’s requirements. The primer and polymer-based applications to be made on the surface ensure better adhesion of the stones.
The adhesive is applied to the surface with a trowel, and the natural stones are placed in the designed form. The gaps in between are filled with filling material, and the surface is cleaned after the stones have dried. The wet bonding system is an economical choice, but due to its limited load-bearing capacity, it can only be used for thin stone slabs.
In the dry system, also known as the mechanical system, the natural stones are fixed to a supporting framework using connection elements made of aluminum, steel, or similar materials. The stones are attached to the connection elements with special clips. This is the safe method for high-rise buildings or heavy and large-sized stones. In addition, security can be increased by using both adhesive and mechanical methods.
Fired Clay-Based Facade Claddings
Throughout architectural history, fired clay-based materials have been used in buildings as sustainable and nature-friendly materials formed by the combination of soil, water, and fire. Offering an aesthetic and versatile façade alternative, these materials provide thermal comfort with their porous structures and are strong in terms of fire resistance. Thanks to firing techniques and additives, fired clay-based materials can be produced in various colors and have high UV resistance. Fired clay-based facade claddings can be classified as ceramic facade cladding, brick facade cladding, and terracotta facade cladding.
Ceramic Facade Cladding
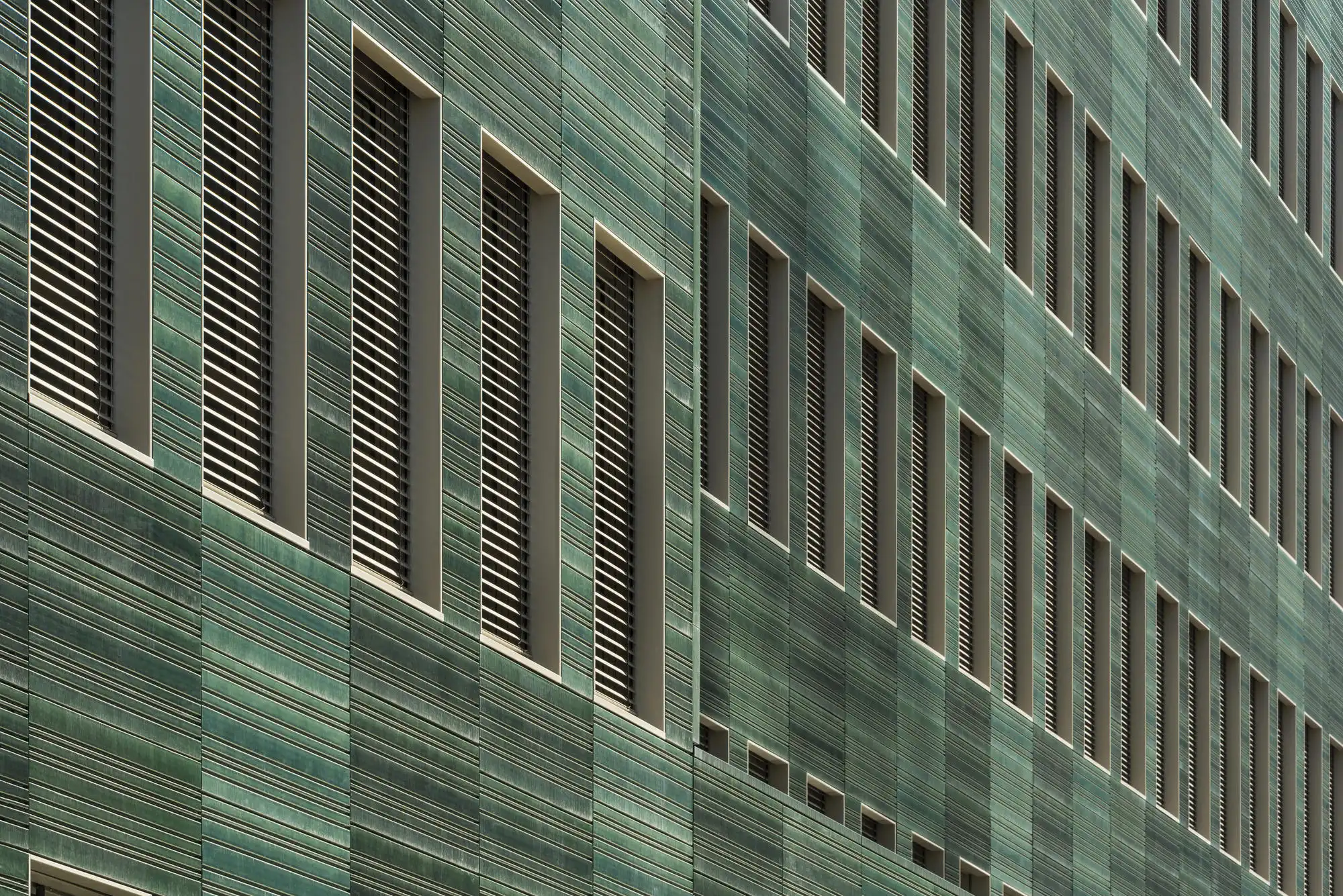
Ceramic, a fired clay-based material preferred for building facades, is produced by firing clay-based components at high temperatures. This coating, which has been frequently preferred as an interior coating for centuries, has found widespread use as an exterior coating after technological developments. Composed mainly of clay, kaolin, quartz, and feldspar, ceramic is fired at temperatures between 1000 and 1300°C.
Offering a wide variety in terms of color and model, ceramic facade coatings are a durable material that is not affected by different climate conditions. Ceramics, which comply with energy efficiency standards, are resistant to fire and have a low maintenance cost. From high-rise residential buildings to commercial structures, hotels, educational institutions, and healthcare facilities, ceramic facade claddings are commonly used. Various types of ceramics can be used in facade cladding, depending on the desired durability and aesthetic appearance.
Ceramic cladding details vary depending on the size, thickness, color, pattern, and type of ceramic selected for the facade. Ceramic sizes, which vary according to the condition of the surface to be applied and the desired appearance, are generally preferred in 60×60 cm, 60×120 cm, and 50×100 cm sizes, while their thicknesses vary between 10 and 20 mm. Different types of ceramics can be used in facade cladding, depending on the durability required and the desired aesthetic. Commonly preferred ceramic types for exterior facades include:
- Porcelain Ceramic: It is frequently preferred as an exterior coating because it is the most dense and has the lowest absorbency.
- Granite Ceramic: Granite ceramic, which takes its name from natural granite in terms of appearance and strength, is resistant to very high pressure and abrasion.
- Ceramic Tile: Ceramic tiles, which are a smaller, modular, and patterned material, offer aesthetic diversity.
- Ventilated Ceramic Panels: They are modular ceramic facade elements specially produced with ventilated systems.
Brick Facade Cladding
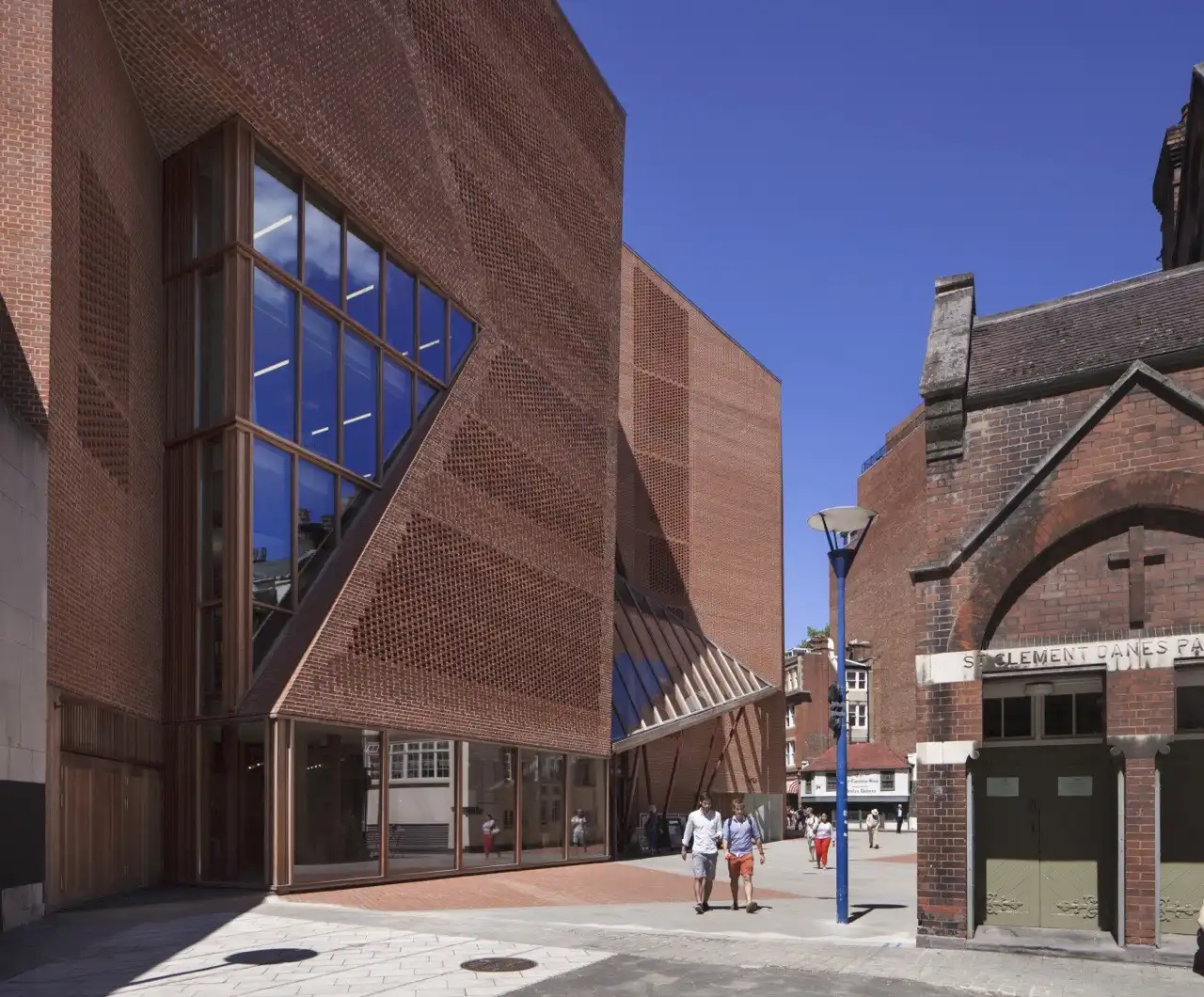
As a clay-based material, brick has been used in the construction industry for thousands of years, serving both as a load-bearing and cladding material. With a wide variety of color and pattern options, facing bricks add aesthetic value to buildings. Bricks, which are a material with high resistance to external factors, protect the structure against rain, snow, wind, and UV rays.
In addition to helping maintain thermal balance inside buildings, facing bricks also offer advantages in terms of sound insulation. Their lightweight and thin structure ensures easy installation, and they require little to no maintenance. Cladding bricks produced from natural materials are also an environmentally friendly option because they are recyclable. Cladding bricks are classified according to their production method, purpose of use, and material properties as follows:
- Clinker Brick: Clinker bricks obtained by firing at extremely high temperatures have a low water absorption rate.
- Fire Bricks: Fire bricks that can withstand heat up to 2800 degrees are a durable material.
- Handmade Bricks: The surfaces of the bricks obtained by firing clay placed in molds by hand are irregular. They offer a natural, nostalgic, and historical appearance.
TerraCotta Facade Cladding
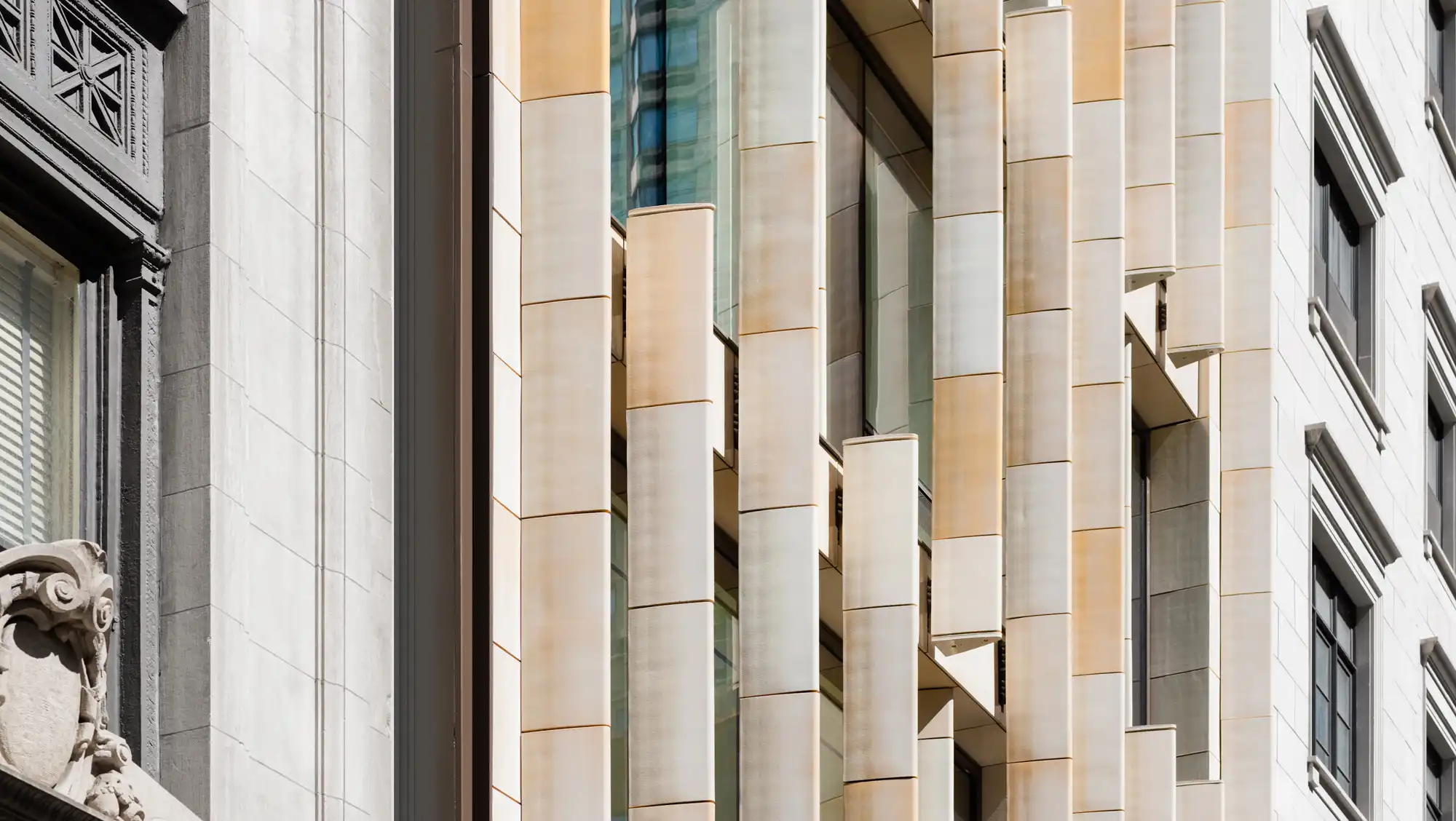
Terracotta, which means baked clay, is a material formed by using natural materials such as clay and kaolin as the main component and baking them at approximately 1000-1100 °C. Terracotta, which provides natural ventilation of facades, has a low water absorption rate and is long-lasting. Terracotta, which can be obtained with a wide variety of color options using pigments found in nature and the colors of the soil and different firing temperatures, does not require maintenance and cleaning.
Terracotta, which has shades such as natural red, brown, yellow, anthracite, and ivory, can also be produced in metallic and special pigments. The material, which provides natural thermal insulation with low thermal conductivity, has high fire resistance. Typically produced in sizes ranging from 1500×4000 mm to 2500×5000 mm, terracotta panels can be cut to custom dimensions during manufacturing due to their homogeneous composition of clay and other natural materials.
Terracotta offers various advantages to users, including resistance to fading and to freeze-thaw cycles, making it suitable for use in all climates. Terracotta facade cladding systems, which have an aesthetic and stylish stance among facade cladding systems, are among the most preferred facade claddings of recent times.
How to Apply Fired-Clay Based Facade Cladding?
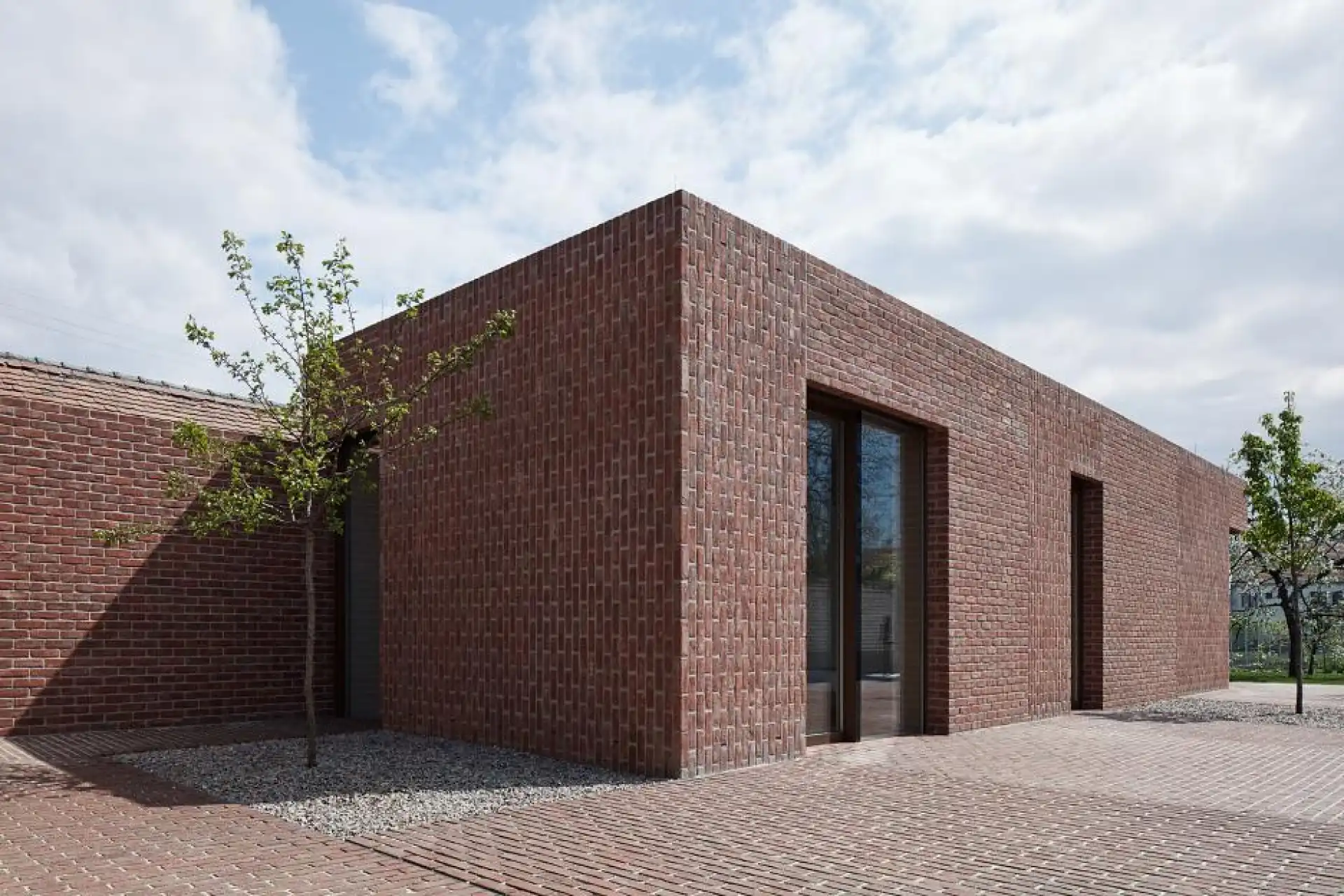
After selecting the appropriate clay-based façade cladding material for the project, the surface to be covered must be checked to ensure it meets the correct conditions. Facade coatings that can be directly bonded to the exterior of the building with the bonding method are placed on the wall in accordance with the design after the powder adhesive is applied to the wall with a trowel. After the entire wall is covered, the gaps should be filled with joint filler material so that the material does not slip and fall, and its shape is not distorted. After the joint material dries, the excess material is cleaned from the surface.
In addition to the adhesive method, a commonly used installation technique is the clip system. The selected clay-based material is attached to specially manufactured aluminum or galvanized steel support profiles using concealed or semi-concealed metal clips. This ensures that no visible fastening elements appear on the façade, resulting in a clean and aesthetically pleasing surface.
Concrete/Cement-Based Facade Claddings
In parallel with the developing technology, various structural elements have started to appear in the sector in addition to classical structural elements. Introduced in the 1990s, cement-based exterior façade claddings combine durability and aesthetics in architecture. These materials offer high fire resistance and excellent sound insulation due to their high density. As a long-lasting and durable cladding solution, cement-based panels allow for a seamless appearance over large surfaces and provide diverse design possibilities. The material, which offers a wide color palette with special pigments, can also be applied to curved, grooved, and 3D embossed designs. Concrete/cement-based facade claddings can be classified as Fiber Cement and Glassfiber Reinforced Concrete.
Fiber Reinforced Cement Panels (Fiber Cement)
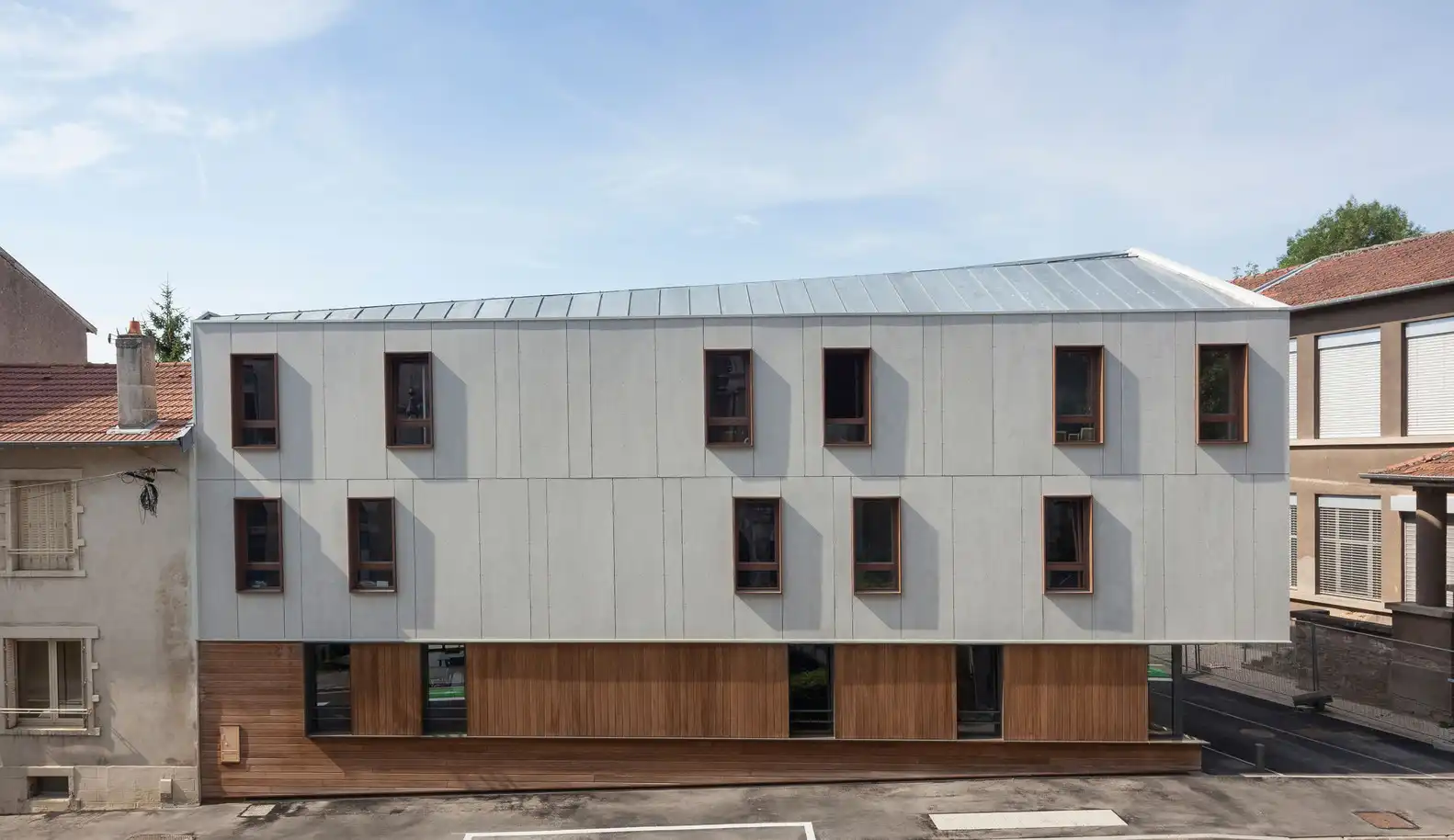
Fiber Cement, which is developed from cement board reinforced with cellulose fiber, is frequently preferred as an exterior cladding. These panels, available in flat sheet form or with various surface textures, are made entirely from natural materials, making them environmentally and human-friendly. The material, which has a wide range of color and pattern options, is resistant to decay and insects. It is a fire-resistant material and helps to extinguish existing fires. Since it is not affected by water, it can be safely used in humid climates, and its resistance to freezing makes it reliable even in the coldest environments. They are produced in standard sizes of 8 mm, 10 mm, and 12 mm thickness, 3050×1250 mm, 3050×1192 mm, 2500×1220 mm, 2500×1250 mm, 2500×1192 mm, and can be selected in sizes suitable for the design.
Glassfiber Reinforced Concrete (GRC)
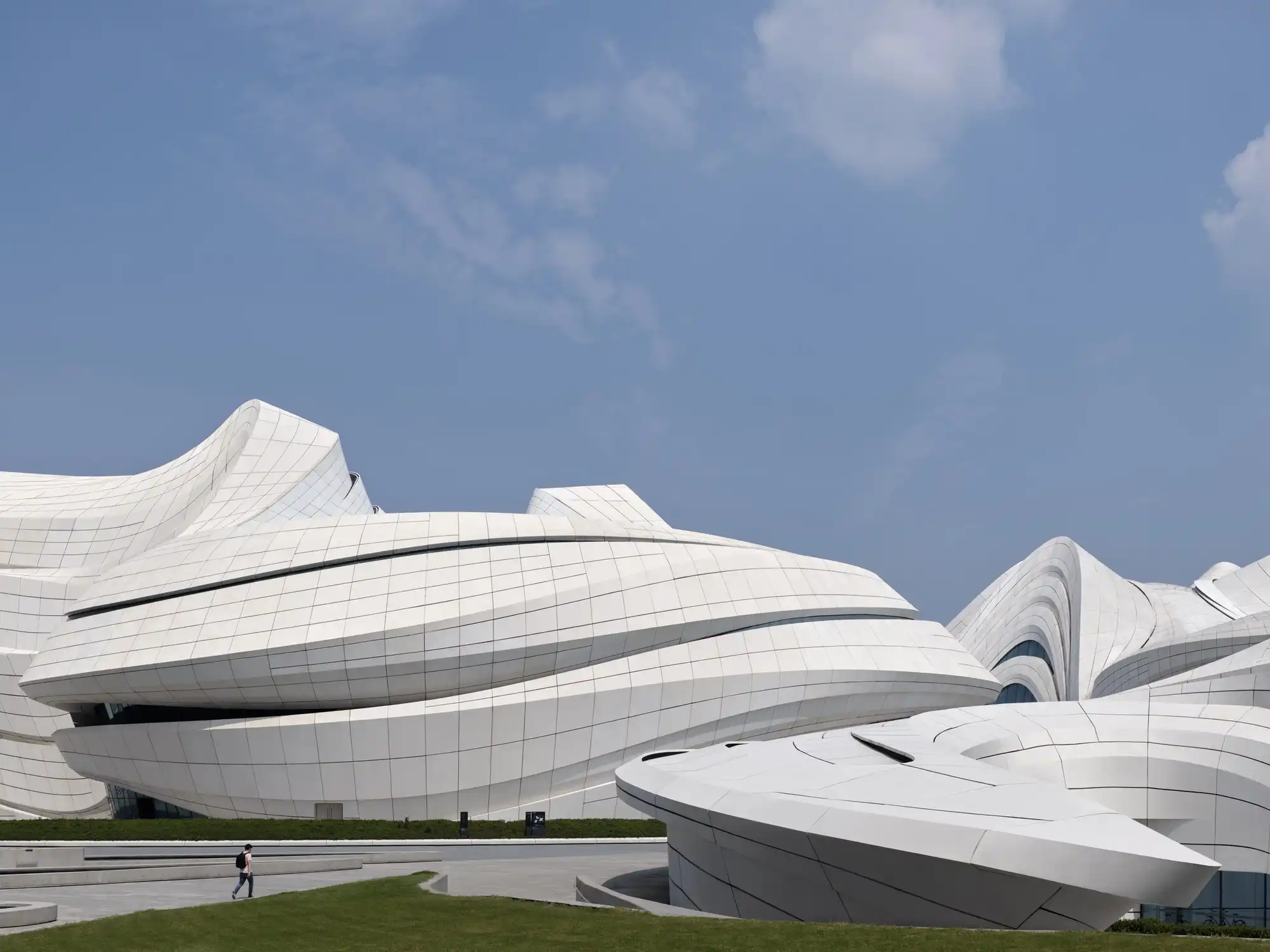
GRC, a high-performance façade element produced by mixing glass fibers into fine-grained concrete, stands out for its durable and long-lasting structure. The material, which is basically made up of white Portland cement, silica sand with high silica content, glass fiber with high alkali resistance, and water components, can be plasticized or different chemicals added according to the size of the structure to be produced.
Due to its lightweight nature, GRC offers ease of production, transportation, and installation. It is highly resistant to earthquakes, provides sound insulation, and is waterproof. GRC, which has higher resistance to impact and pressure compared to traditional concretes, has rich design options in terms of aesthetics.
How to Apply Concrete/Cement-Based Facade Cladding?
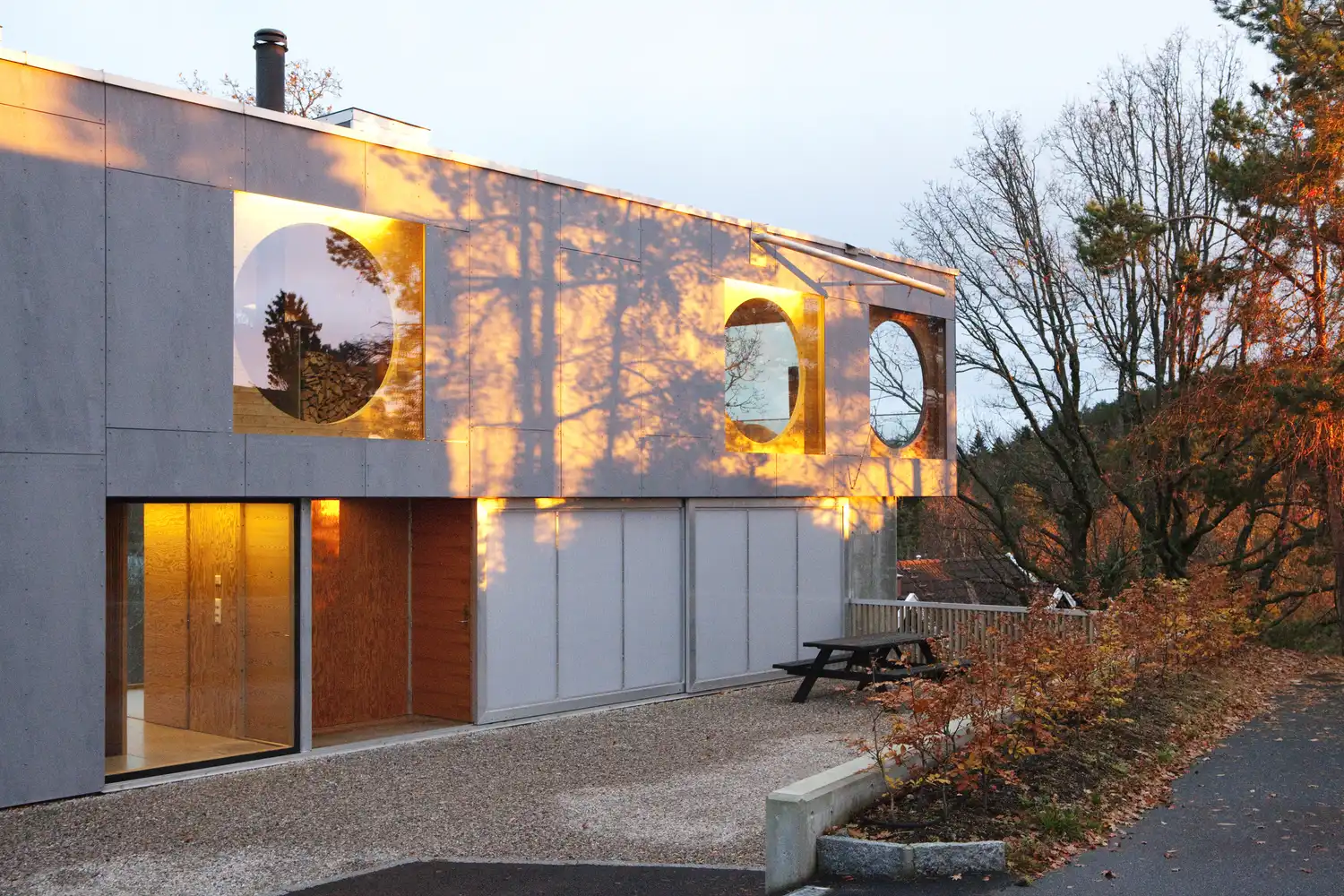
Concrete and Cement-Based Façade Cladding is mounted onto a steel or wooden substructure using mechanical or adhesive methods. First of all, a solid infrastructure must be created for panel assembly. Then, the panels cut to appropriate dimensions for the project are ready for coating. The panels are attached to the surface using screws, dowels, or special adhesives on the suitable substructure. For long-lasting use and water tightness, joint fillers must be filled with an appropriate material. The top of the panels can be painted in the selected color if desired. At the same time, the panels can be fixed to the carrier frame with steel anchors and consoles. This method allows it to be designed as a ventilated system.
Metal Sheet Façade Cladding

Metal facade cladding, which brings together aesthetics, stance, and functionality in modern architecture, is often preferred on facades. Metal cladding, which gives buildings a stylish appearance, is highly resistant to adverse weather conditions, UV rays, and corrosion. These materials, which have high fire resistance, do not increase the load of the building with their lightweight structure and protect structural integrity.
Metal sheets, which can be easily installed and are easy to maintain, provide efficiency in terms of time and cost. Offering options such as flat, perforated, and embossed designs, metal sheet façades allow for a wide variety of creative façade designs, enabling minimal, sharp-lined, high-performance, and technological buildings to benefit from both aesthetic and functional advantages. The types of metal materials are listed as follows:
- Aluminum: Lightweight and easily processed, aluminum is resistant to corrosion.
- Stainless Steel: It is a durable material and allows for shiny surfaces.
- Copper: Copper, which oxidizes and changes color over time, is often preferred in historical structures.
- Titanium: Titanium, a very light and durable material, is quite costly compared to other metals.
How to Apply Metal Sheet Façade Cladding?
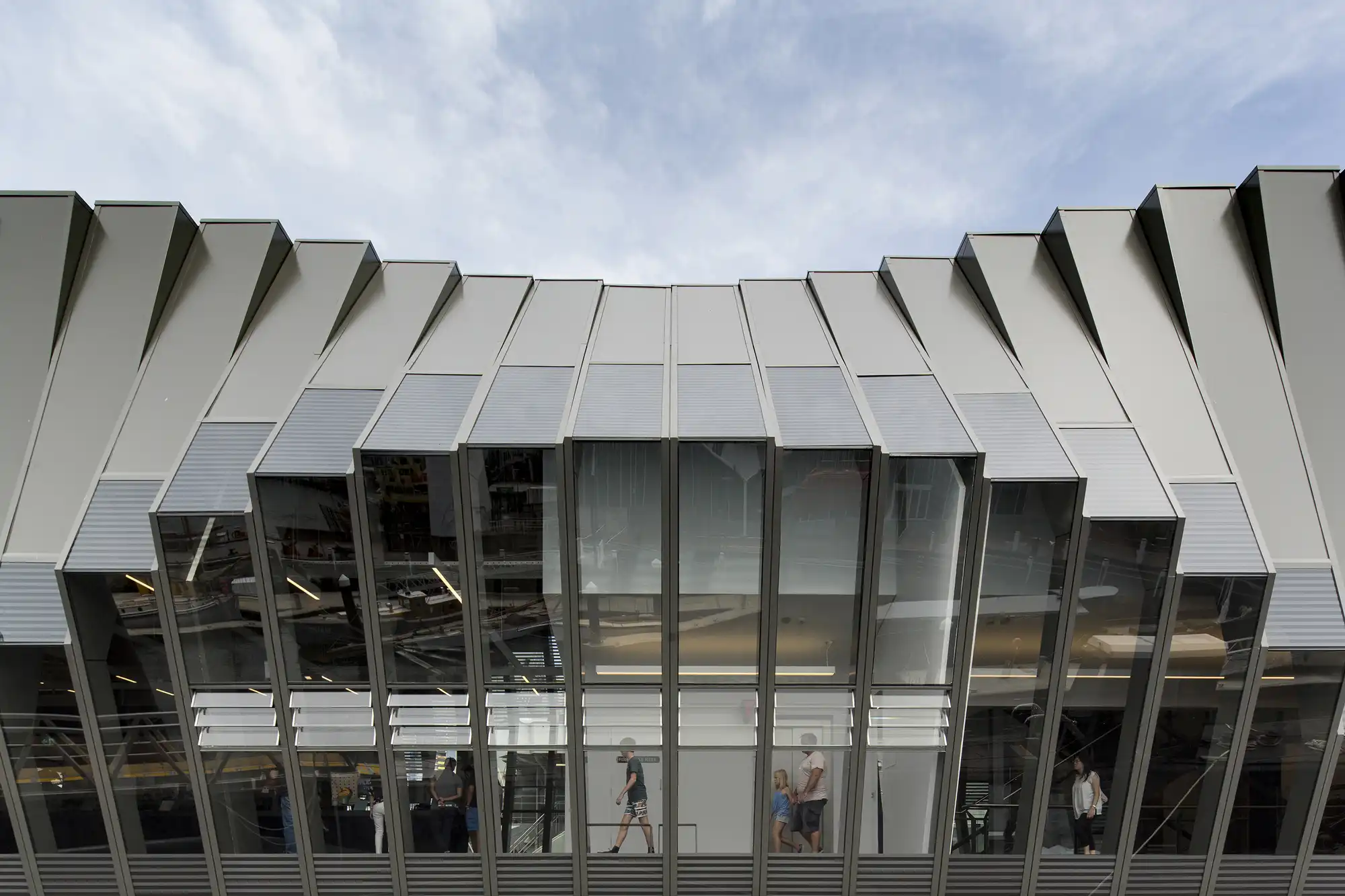
Before applying metal facade cladding, it is very important that the surface to be applied is smooth and clean. Choosing the right material for the use of metal materials in facade cladding is also very important. Appropriate metal sheets should be preferred by considering the structural features of the building, climate conditions, and aesthetic preferences.
Metal sheets, cut and shaped to the correct dimensions for the building’s surface, have insulation materials placed underneath, enhancing energy efficiency. The prepared metal sheets can be adhered to the façade using structural silicones. For larger panel installations, the panels are mounted on the surface with anchors, clip systems, and rail carriers. After cladding, the gaps between the sheets and the edge points are filled to prevent air and water leakage, thereby increasing the durability of the cladding.
Glass Curtain Walls
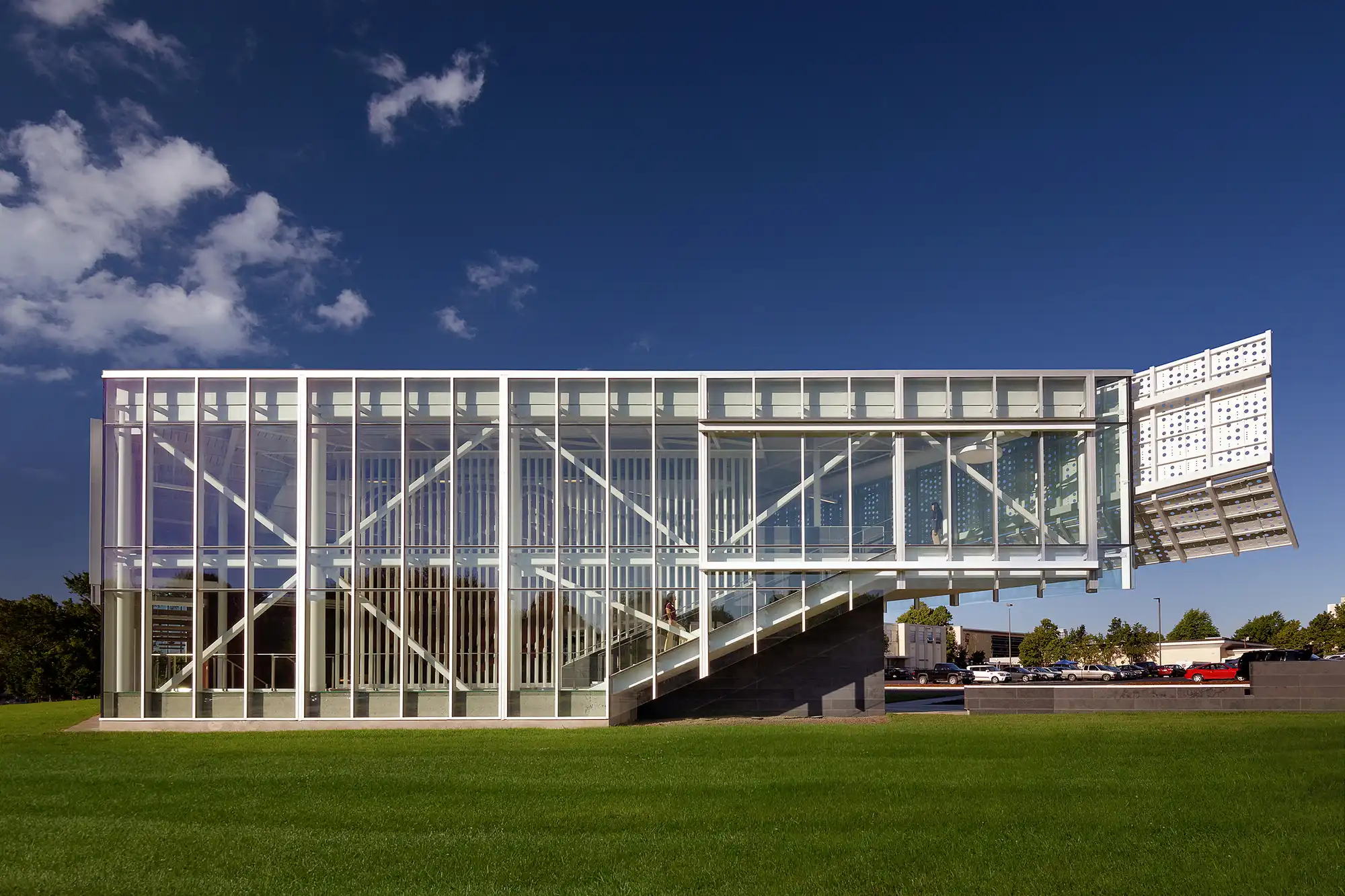
Glass curtain walls, which provide a modern and transparent appearance in buildings, can achieve various aesthetic effects with different types of glass, colors, and surface treatments. Although the main and intermediate carrier elements, made of aluminum material on the outer surface of the building, are more durable, they do not have a carrier feature on their own. The aesthetic concerns of modern architecture have necessitated innovative solutions and the use of glass, aluminum, and metal, which have found more place in architecture, especially since the 19th century, and have increased the preference rate of curtain walls.
If you don’t want to miss the innovative solutions developing in architecture, learn with PAACADEMY. By joining PAACADEMY’s workshops, you can master advanced parametric design tools from leading industry experts, learn how to integrate artificial intelligence into design workflows, and leverage computational design in architecture.
Glass curtain walls were first used in the Oriel Chambers building in Liverpool, England. Designed by architect Peter Ellis in 1864, this building demolished the traditional stone facade concept and paved the way for glass curtain wall cladding. The glass curtain wall system, which protects the building from rain, kinetic energy, and capillary water absorption, is also effective against sunlight. It allows for the use of insulation, contributing to energy savings and correcting potential shape defects. With no color or texture distortion, maintenance and repairs are minimized. Glass curtain wall facades, which increase the quality of space with light transmittance, are suitable for high-rise buildings with their lightweight structure. However, it requires a high investment cost, and if no shading is provided, the interior can overheat in the summer months.
How to Apply Glass Curtain Walls?
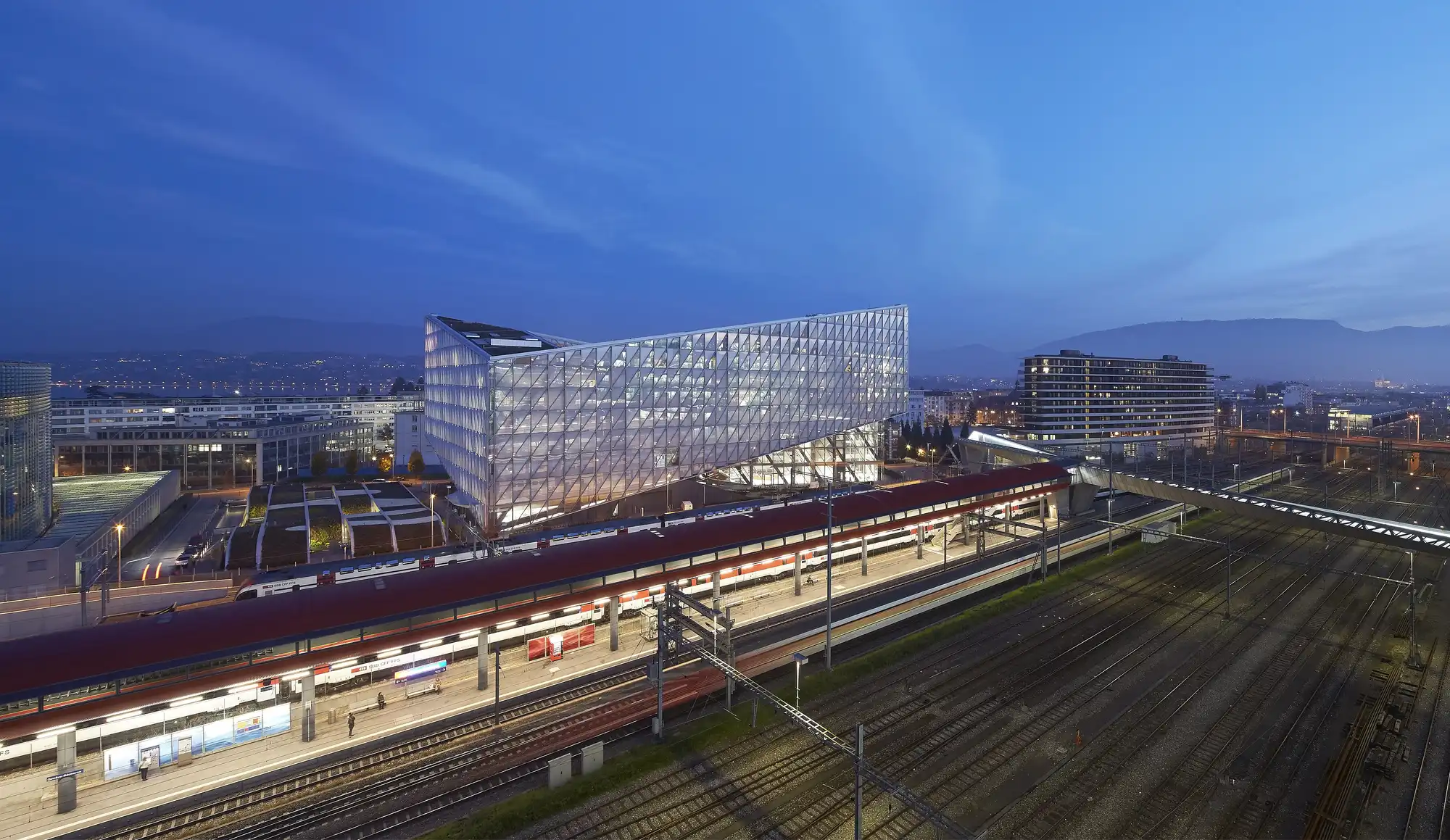
Panel dimensions, connections, and modules that can be modeled with the help of BIM programs provide convenience before application. Aluminum frames, glass, and accessories are produced in the factory according to the design, and the modules are prepared. The type of glass to be applied should be selected in the designed color and pattern, considering the light transmittance suitable for the project.
Reflective-coated glass is commonly used in commercial buildings with curtain walls, as it conceals the back of the façade during the daytime and creates a homogeneous exterior. In contrast, buildings where the view is important, such as residential buildings and shop windows, typically use low-emissivity solar control glass. The panels carried to the construction site are applied to the facade with carrier anchors and coating elements by crane.
Facade claddings, which are one of the most distinctive elements of a building and give the structure its identity, directly affect the design of the structure, architectural language, and user experience. Along with traditional materials such as stone and brick, the development of technology has introduced modern façade materials such as glass and metal in contemporary architecture.
The correct façade cladding, chosen in line with the design, influences both the aesthetics and performance of the building. All surfaces of a façade can be covered with a single façade material, or it can be completed by selecting several materials that work well together.
Leave a comment