Due to their special geometry, saddle-surface structures allow for the construction of very material-efficient and lightweight roofs. There is a long history of such constructions, mostly built from concrete, which requires cost and labor-intensive formwork structures for the casting. Furthermore, it is challenging to integrate openings for natural lighting in the concrete shells.
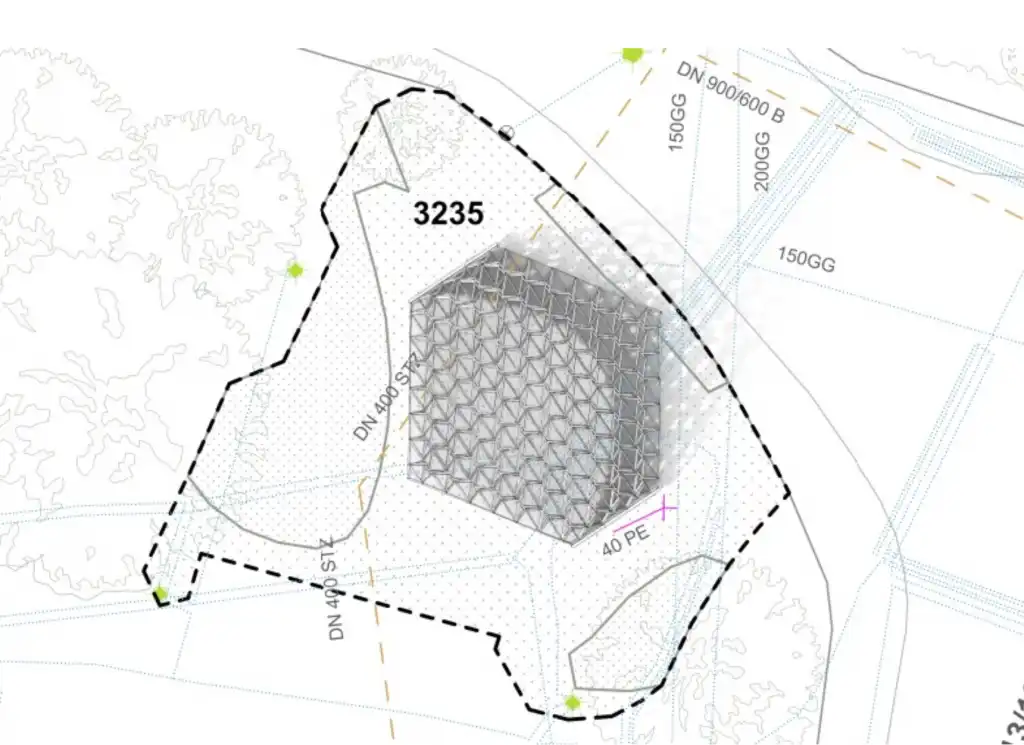
Considering modern challenges in the building industry, such as the urgent need for more renewable and natural materials like naturally grown local hardwoods, the assembly of larger structures from a large amount of short wood elements is necessary either way due to the wood properties (especially for deciduous / hardwood species, which do not grow as straight as spruce trees).
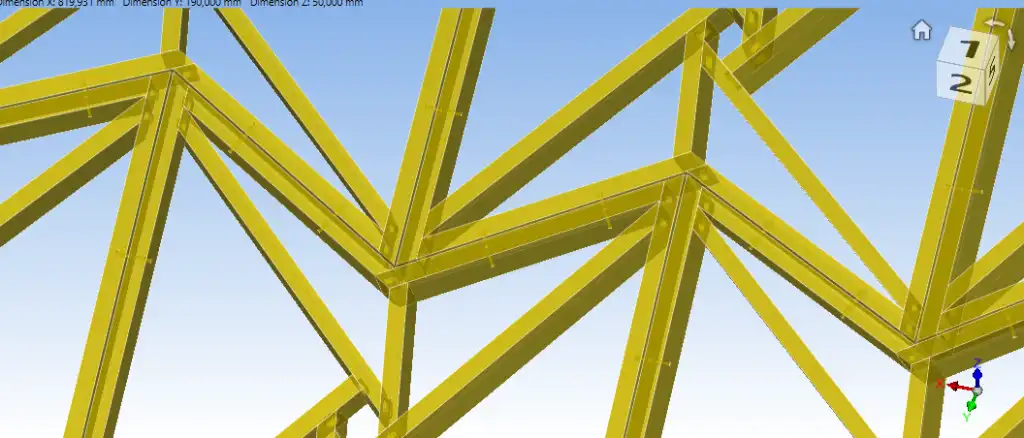
And since robotic fabrication and CNC machining are widely available, material-efficient geometries such as shells and saddle surfaces could help to reduce the amount of material for larger spanning roofs – especially considering that such roof shapes primarily load the joints in compression, which allows for more simple joints, with less steel needed. This is particularly important when working with wood species with high (corrosive) acidity, such as Castanea sativa or many of the hardwoods that are challenging to glue.
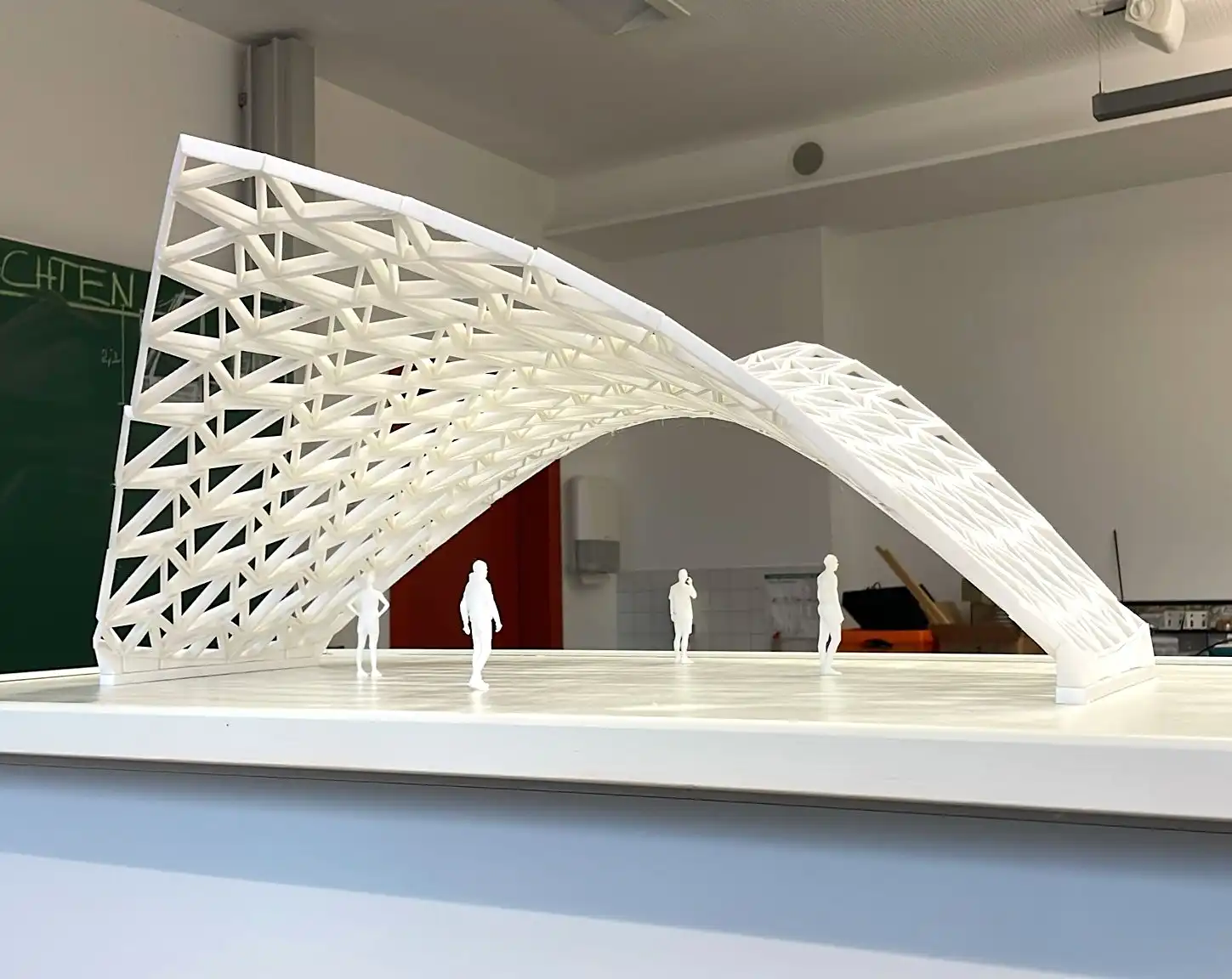
In our previous research demonstrators, the DTC team had already developed a system that allows for the construction of large-span roofs with short individual wood pieces. This allows for the use of lower-grade wood elements, especially for the use of natural hardwood, which is generally limited to smaller dimensions and shorter lengths.
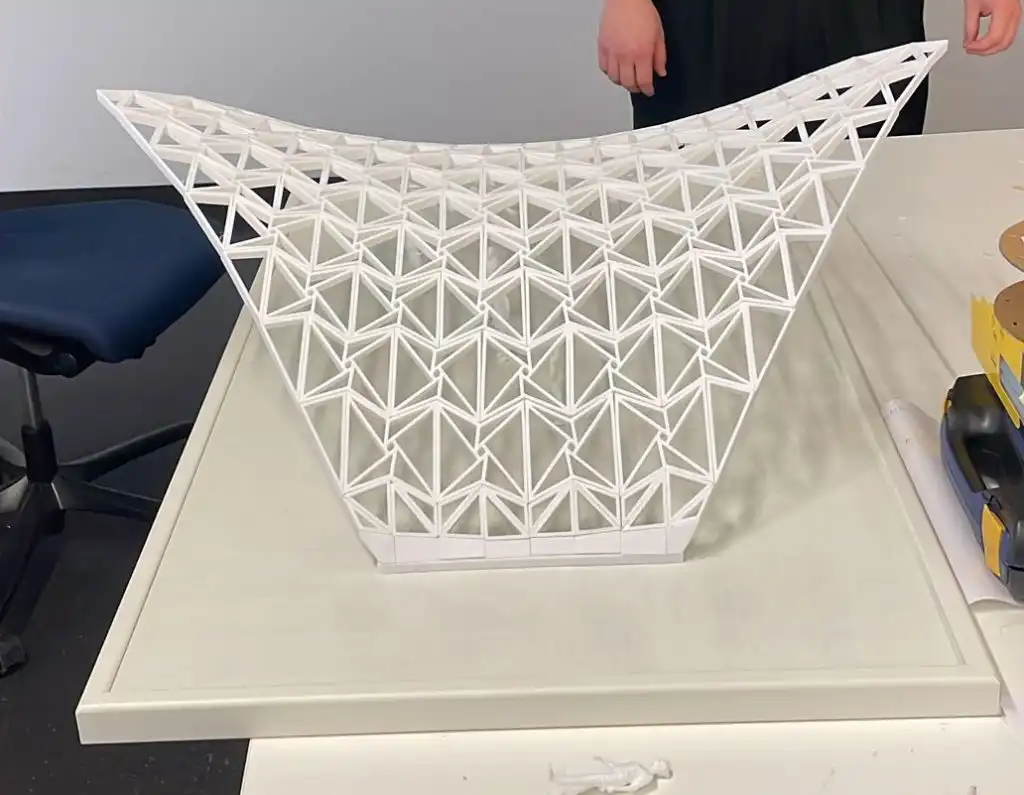
With a 15m column-free span, the TSI Chestnut Hypar Demonstrator is currently the largest-span roof structure made from natural Castanea sativa wood (sweet chestnut). The geometry of the structure combines an anticlastic planar hexagonal (P-Hex) topology with reciprocal cross-bracing members.
The Castanea Sativa wood has outstanding strength properties, but most importantly, the trees are highly resistant to a warm and dry climate. Therefore, they have become an important species to help stabilize forests that are struggling with climate change.

The demonstrator is part of the BMEL FNR-funded research project. TSI shows new possibilities with digital fabrication integration and lesser-used, climate-change resilient wood species such as Castanea Sativa.
Thanks to the support from the city of Friedberg, this research demonstrator will be realized as a permanent structure since the site, foundations, and the cost of permits were covered.
Castanea Sativa Hypar Gridshell Project Details:
Completion year: 2025
Project Team: Research & Development / Digital Timber Construction Research Group / TTZ Digital Planning and Building Aichach, Prof. Dr. C. Robeller, Dr. H. Karimian, A. Adelzadeh, K. Ahlund, Structural Engineering: str-ucture GmbH, Checking Engineers: Z-MI GmbH Regensburg, Timber Construction: Züblin Timber Aichach and Bradl Holzbau. Foot details: Sulzer Metallverarbeitung GmbH.
The project description is provided by the Digital Timber Construction (DTC).
Leave a comment